1편. 광범위한 재료 특성을 포괄하는 건식 분말 압축
[기고: 정동준 쿠어스텍 생산기술팀 팀장]세라믹 재료는 다양한 전자기적 및 물리적 특징을 갖고 있다. 많은 세라믹 재료들은 고온의 환경을 견딜 수 있는 우수한 내열성을 가지고 있고 내화학성이 높아 반응성이 높은 화학약품 또는 화학물질에 의한 부식을 막아주는 소재로 사용된다. 구성 성분에 따라 절연성을 가지는 소재부터 초전도성을 가지는 소재까지 다양한 전자기적 특징을 갖고 있다.
필자는 이번 기고를 통해서 그 중에서도 활용성이 높은 테크니컬 세라믹의 특징과 그 가공법에 대해 3회에 걸쳐 소개한다.
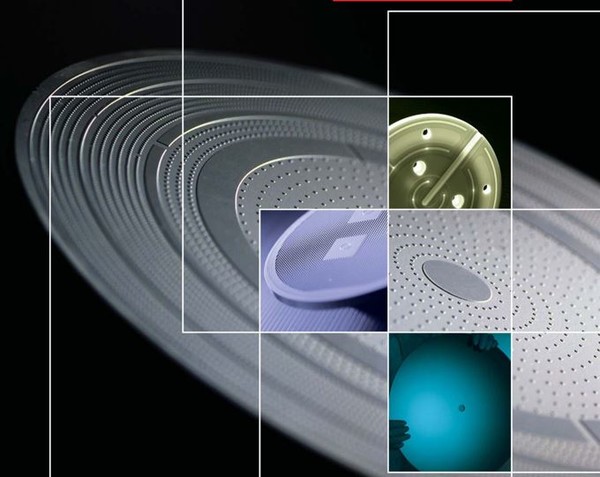
고성능 또는 엔지니어링 세라믹이라고도 불리는 테크니컬 세라믹은 물리적 특성과 열 특성이 결합돼 다른 금속재료나 유기재료가 구현하지 못하는 점을 대체할 수 있는 매우 크고 다양한 특성을 갖고 있는 무기(inorganic) 세라믹 재료다. 테크니컬 세라믹은 성형, 소성, 그리고 마무리 옵션에 따라 그 활용도가 무궁무진하다. 쿠어스텍은 다양한 마무리 및 가공 옵션, 맞춤형 디자인, 높은 정밀도를 가진 프로세스를 통해 테크니컬 세라믹의 무한한 가능성을 확장시키고 있다.
건식 분말 압축이란
첫 번째 성형 방법은 세 가지 압축 프로세스를 포괄하는 건식 분말 압축(Dry Powder Compaction)이다. 세 가지 압축 프로세스에는 건식 압축, 등압 압축 및 롤 압축이 포함된다. 건식 분말 압축용 원료는 탈륨 분말과 유사한 특성으로 유동성이 좋지 않아 제조에 부적합하다. 이를 극복하기 위해 분말이 여전히 건조할 때 액체처럼 흐르는 공급 원료로 변환한다. 이런 식으로 분말 처리 과정을 거치면 건식 분말 압축 공정에서 사용할 수 있는 상태가 된다.
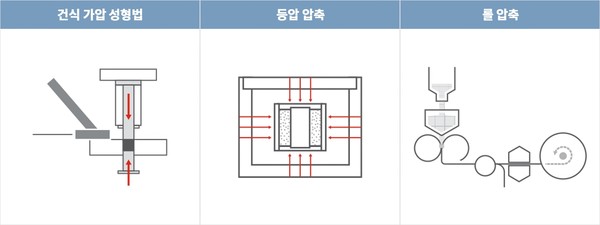
건식 가압 성형법
대량의 맞춤형 구성 요소가 필요한 경우 건식 압착이 탁월한 방법이다. 건식 압착 공구(tooling)에는 다이, 이젝터, 펀치 및 필 슈(fill shoe)가 포함돼 있다. 필 슈는 가압 입자를 몰드에 주입하는데 사용되는 부품이다. 가압 작업은 필 슈가 세라믹 분말을 다이 캐비티(cavity)에 침전시킨 후 수축해 재료를 다이 상단과 수평으로 맞출 때 시작된다. 다이 캐비티는 성형 중에 생기는 다이의 속이 비거나 오목한 부분을 일컫는다. 다이 캐비티 아래에 있는 이젝터(ejector)가 하강해 다이 표면 아래에 분말이 떨어지면 펀치가 다이 캐비티로 이동한다. 펀치와 이젝터가 간극을 좁혀 파우더를 압축한다. 전체 압축이 완료되면 펀치가 수축되고 이젝터가 눌린 부품을 다이에서 밀어낸다. 마지막으로 주입구가 다이 위로 이동해 부품을 공구에서 밀어내고 세라믹 분말을 다이에 침전시키는 사이클이 반복된다.
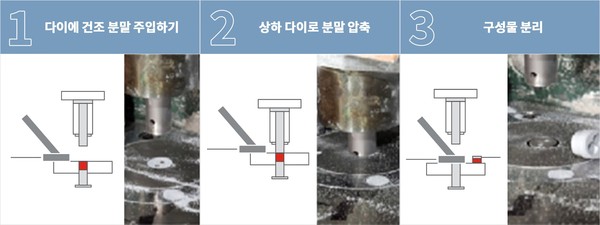
압착 후 산화물(oxide) 성분은 일반적으로 별도의 탈지 작업이 필요하지 않다. 사용되는 바인더의 양이 적고 압축된 부품은 소결 킬른(sintering kiln) 프로파일의 전단부에서 바인더 연소를 용이하게 하기 위해 여전히 다공성(porosity)을 가지고 있기 때문이다. 비산화물의 경우 소결 킬른(sintering kiln) 환경이 바인더 제거에 적합하지 않아 별도의 바인더 소진 단계가 필요할 수 있다. 건식 가압은 대량 생산을 위해 쉽게 자동화가 가능하며 간단한 모양부터 심봉(core rod)과 금형 인서트(die insert)가 펀치와 인젝터와 독립적으로 움직이는 고도로 복잡한 형상까지 생산할 수 있다.
등압 압축성형(ISOSTATIC PRESSING)
등압 압축은 세라믹 분말을 압축하면서 모든 방향으로 동일한 압력을 가하는 방식으로 소량 및 중간 규모 생산에 매우 적합하며 일부 대형 기하학적인 모형을 생산하는데도 유용하다. 등압 압축은 모든 압축이 한 방향으로 이뤄지는 건식 압축과 달리 세 방향에 나눠 진행된다.
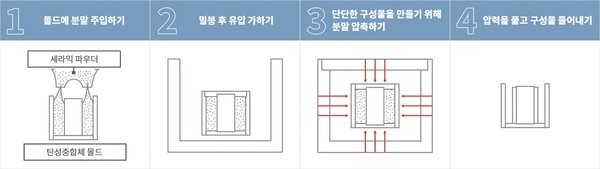
건식 가압에 사용되는 것과 동일한 유형의 건조 세라믹 분말이 등압 프레스에 사용된다. 그러나 때때로 분말은 공정의 효율성을 높이기 위해 재료 특성 차이를 최소화하도록 설계된다. 등압 압축 성형에서는 탄성 중합체 자루(elastomeric sack)가 공구 또는 몰드의 역할을 수행한다. 몰드는 세라믹 분말로 채워져 밀봉되고 액체(일반적으로 물)가 둘러진 상태로 압력 챔버(pressure chamber) 내부에 배치된다. 액체 매개체가 압력을 받으며 몰드로 분말을 압축시킨다. 테크니컬 세라믹 튜브를 압착하기 위해 고무 주머니 내부에 스틸 아버(steel arbor)를 배치해 내부 표면을 만든다. 유압이 모든 방향에서 동일하기 때문에 압분체 밀도(green density)가 매우 균일한 부품을 만들 수 있다. 이는 소결(sintering) 시 수축 제어 및 균일성에 유리하게 작용한다. 쿠어스텍은 필요한 생산량과 다짐 압력(compaction pressure)에 따라 건식 등방압(dry bag press)과 습식 등방압(wet bag press)을 사용하고 있다.
건식 등방압과 습식 등방압의 차이
낮은 수준에서 중간 수준의 생산 속도의 경우 일반적으로 습식 등압착이 선호된다. 클러스터 백을 사용하면 동일한 사이클 동안 더 많은 부품을 동시에 압축할 수 있어 생산률을 더 높일 수 있다. 액체가 탄성 중합체(elastomeric) 몰드 주위를 채우기 때문에 자루(sack)가 어떻게 생겼든 간에 몰드를 수용할 수 있을 만큼 충분히 큰 프레스를 사용할 수 있다. 반대로, 건식 등압법은 더 큰 부피의 등압 프레스에 사용되며 이를 위해 특별히 설계된 공구만 사용할 수 있다. 이 방법은 액체를 억제하는 프레스 내부의 고무 주머니를 사용한다. 프레스 공구의 외부는 프레스 내부의 내부 자루에 맞도록 특별히 설계돼야 한다. 압력이 가해지면 외부 자루(프레스)가 내부 자루(몰드)를 눌러 분말을 압축한다. 공구가 건조한 상태를 유지하기 때문에 더 빠른 프레스 사이클이 가능하고 더 쉽게 자동화할 수 있다. 대량 생산과 다중 캐비티 생산에는 전자동 건식 등압법이 사용되기도 한다.
롤 압축(ROLL COMPACTION)
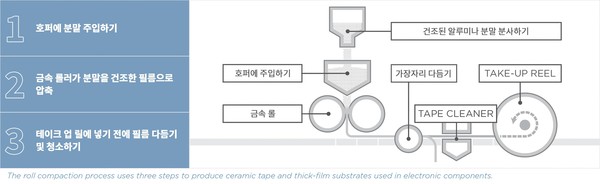
건식 분말 압축의 세 번째 방법은 롤 압축이다. 이 공정은 세라믹 기판을 제조하는 데 가장 많이 사용된다. 추가 바인더를 사용해 구성물을 고가소성(high plastic)으로 만드는 분무 건조된 세라믹 분말은 2개의 롤러 사이에서 연속적으로 움직인다. 가소화된 세라믹 재료는 롤러 사이에서 압착돼 원하는 두께로 압착된다. 일반적으로 테이프의 가장자리는 재료의 가소성 때문에 사용할 수 없기 때문에 절단돼 재활용된다. 그런 다음 압축된 재료를 테이크업 릴(take-up reel)에 롤링시킨 후 바인더 제거 및 소결(sintering)을 위해 압축된 물질을 풀어서 킬른(kiln)을 통해 내보낸다.
세라믹 제조 공정은 생산 수량 및 가공 원료의 특성에 따라 다양하게 적용된다. 그만큼 재료의 특성을 이해하고 올바른 프로세스를 선택해 가공하는 것도 중요하다. 다음 회차에서는 습식 가공 프로세스와 가소성형을 통해 더욱 다양한 세라믹 재료의 특성과 공정 방식을 파악하려고 한다.
그래도 삭제하시겠습니까?