2편: 실생활에서 활용되는 세라믹 제품 생산 위한 성형법
[기고: 정동준 쿠어스텍 생산기술팀 팀장]
![[사진=게티이미지뱅크]](https://cdn.epnc.co.kr/news/photo/202305/233162_234447_1536.jpg)
세라믹 재료는 다양한 전자기적 및 물리적 특징을 갖고 있다. 많은 세라믹 재료들은 고온의 환경을 견딜 수 있는 우수한 내열성을 가지고 있다. 내화학성이 높아 반응성이 높은 화학약품 또는 화학물질에 의한 부식을 막아주는 소재로 사용된다. 구성 성분에 따라 절연성을 가지는 소재부터 초전도성을 가지는 소재까지 다양한 전자기적 특징을 갖고 있다.
지난 회차에서는 광범위한 재료 특성을 포괄하는 가공법인 건식 분말 압축법과 함께 다양한 세라믹 재료와 특성에 대해서 알아봤다. 이번에는 방탄복, 세라믹 튜브, 점화기 등 실생활에서 보다 자주 사용되는 세라믹 재료가 어떤 재료 특성을 지니며 이러한 재료를 성형하기 위해 사용되는 습식 성형 방법과 가소성형에 대해서 알아보려고 한다.
습식 성형 방법
이 프로세스는 점화기에서 방탄복, 전자 장치용 기판(subtrate)에 이르는 다양한 구성품을 제조하는데 사용된다. 습식 가공은 슬립(slip)캐스팅과 테이프 캐스팅 두 가지 범주로 나뉜다.
슬립 캐스팅
도자기를 만드는 데 사용되는 기술인 슬립 캐스팅(Slip Casting)은 갑옷과 같은 테크니컬 세라믹을 형성하는데도 사용된다. 특히 군인과 응급 의료원의 몸을 보호하는 방탄복 생산에 주로 사용된다.
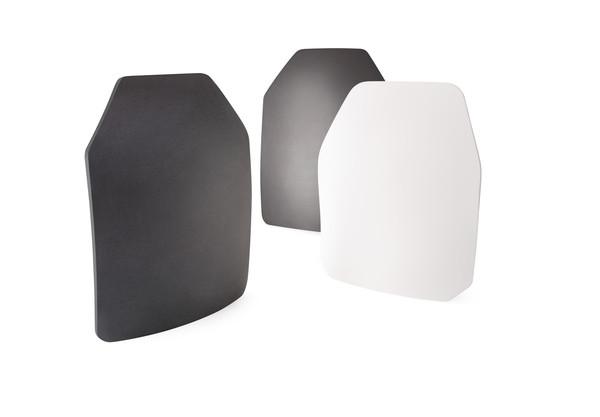
이 공정은 액체 캐리어 내부에 세라믹 분말을 분산시켜 슬러리 또는 슬립을 만든 다음 다공성 주형으로 주조하는 것으로 시작된다. 몰드의 모세관력(capillary force)은 액체를 다공성(porosity)으로 끌어당기고 기공보다 큰 세라믹 입자가 몰드의 벽에 부딪혀 두께가 쌓이게 된다.
목표 두께에 도달하면 여분의 슬립이 배출되며 가마에서 소성할 준비가 된 녹색 구성요소(green component)가 남는다. 더 많은 생산을 위해 외부 압력 작용을 통해 주조 속도가 가속된다. 이를 ‘압력 주조’라고 한다. 높은 주조 압력에 필요한 강도를 제공하기 위해 다공성 플라스틱 주형이 주로 사용된다.
테이프 캐스팅
고급 박막 세라믹 기판의 경우 테이프 캐스팅이 선호되는 방법이다. 두꺼운 필름 테이프에 사용되는 롤 압축과 달리 이 프로세스는 석판(lithography) 기반 전자 회로에 더 적합하다. 이 프로세스는 가스 난방 시스템, 오븐 및 레인지, 건조기 등에 사용되는 점화기에 필요한 구성 요소를 제조하는 데도 사용된다.
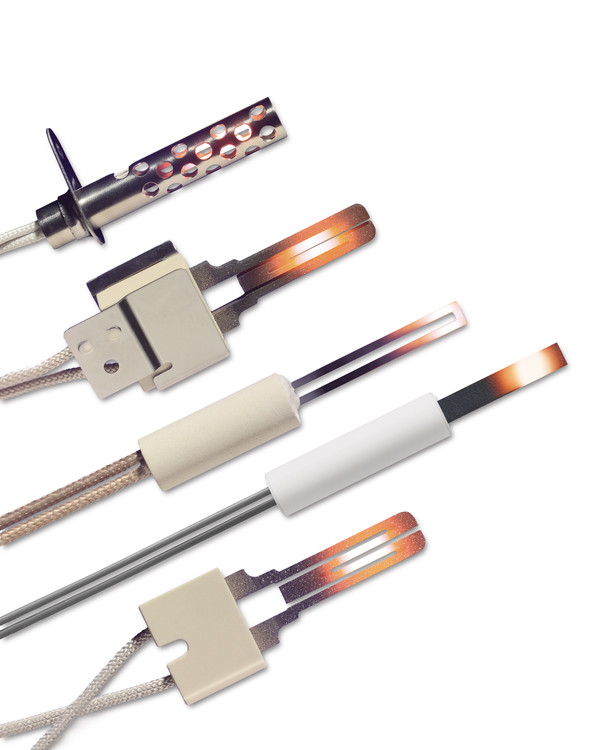
테이프 캐스팅 공정은 슬립 캐스팅과 유사하다. 테이프를 만들기 위해 세라믹 슬러리를 움직이는 마일라(Mylar) 시트에 주조한다. 마일라 슬러리를 훑개 (doctor blade) 아래로 이동해 테이프 두께를 설정한다. 그런 다음 테이프는 릴에 추가되어 가마에 소성하도록 보내진다.
가소 성형 (plastic forming)
테크니컬 세라믹 성형 방법의 세 번째 범주는 플라스틱 성형이다. 가소 성형에서 공급원료는 플라스틱 매개체(medium)에 분산된 세라믹 분말이다. 그 다음 이 혼합물에 압력을 가해 다이에 넣어 부품을 성형한다. 가소 성형에는 압출 성형, 사출 성형 그리고 습식 가공의 세 가지 다른 가공 방법이 존재한다.
압출 성형(Extrusion)
압출 성형은 다양한 산업 응용 분야를 위한 고성능 테크니컬 세라믹 튜브 및 막대를 제조하는 데 사용된다. 압출 성형은 어린 시절 즐겨하던 반죽 놀이와 비슷하다. 길고 독특한 모양을 만들기 위해 반죽 사이로 플라스틱 막대를 밀어넣는 것과 같다.
압출 성형은 튜브, 막대(rod)와 같이 가늘고 긴 가로 세로 비율이 높은 구성 요소에 적합하다. 쿠어스텍은 다양한 용도로 사용할 수 있는 기술적인 세라믹 튜브와 로드를 수백 개의 표준 모양과 크기로 생산할 수 있을 뿐만 아니라 고객 맞춤형 압출도 진행이 가능하다.
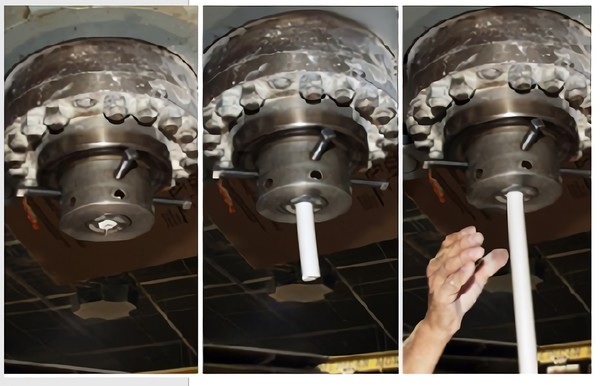
압출은 연속 공정이므로 단면이 일정한 길고 직선적인 구성요소에 이상적이다. 이 과정은 플라스틱-세라믹 재료 혼합물에서 시작된다. 이 플라스틱 혼합물은 압출 다이를 통해 통과된 다음 소성 전에 다루기 쉽도록 고체화다. 압출은 연속적인 공정이지만, 일반적으로 압출은 소성 전에 목표 길이로 절단된다.
사출 성형 (Injection)
사출 성형은 대량 생산이 필요한 복잡한 3차원 형상에 적합하다. 다른 성형 방법으로 필요한 형상을 생산할 수 없는 경우 소량 생산에도 사용되기도 한다.
기본적으로 세라믹 분말이 꽉 채워진 플라스틱을 성형한 후 성형 후 플라스틱 캐리어를 제거한다. 이 때 사용되는 조형기는 테크니컬 세라믹에 사용되는 것과 동일하다. 하지만 세라믹 분말은 연마성이 강하기 때문에 사출 성형에 사용되는 기계는 마모 구성 요소를 매우 단단한 재료로 대체하여 마모에 저항하고 마모 수명을 향상시킨다.
공정은 플라스틱-세라믹 혼합물이 피드 스크류 챔버(feed screw chamber)로 주입되면서 시작한다. 피드 스크류는 자재를 피트 튜브를 통해 몰드 캐비티(mold cavity)로 밀어 넣는다. 모양이 만들어지면 다이가 구성물을 방출하기 위해 분리된다.
세라믹 사출 성형의 경우 주입된 구성물을 플라스틱 없이 이전 상태로 되돌리기 위해 디바인딩 작업이 필수적이다. 플라스틱을 제거하면 여과와 같은 특성을 필요로 하는 어플리케이션을 위한 구성물의 다공성이 열린다.
습식 성형 (Wet molding)
습식 성형에서 세라믹 재료는 물과 혼합돼 점토와 유사한 특성을 가진다. 그런 다음 재료를 몰드 압반(platens) 사이에 두고 석고(plaster)로 성형한 후 압축하여 모양을 만든다. 석고는 압축 도중 발생하는 구성물로부터 배출되는 과도한 수분을 흡수하는 역할을 한다.
위에서 살펴본 것처럼 테크니컬 세라믹 활용은 무궁무진하다. 멀게만 느껴지는 우주산업, 치밀하게 느껴지는 반도체에도 활용되지만 갑옷, 방탄복, 가스레인지 점화기, 세라믹 튜브 등 우리의 일상 속에서 찾아볼 수 있는 제품도 많다. 다음 회차에서는 세라믹 공정의 꽃이라고 할 수 있는 가마 공정에 대해서 알아보려고 한다.
그래도 삭제하시겠습니까?