- 일본 전기 유리 : 30층 이상의 다층 반사 방지막을 이용해서 투과도 99.5%의 투명 유리 개발
- 일본 Henan Succeed New Energy Material Co Ltd : 100nm 두께의 SiO2로 이루어진 반사 방지막을 이용해서 투과도 97%를 달성
- 미국 3M : 23μm 두께의 fluoropolymer을 기반으로 한 시트를 개발하였는데, 태양 전지 패널에 직접적으로 붙일 수 있다. 이 박막은 수분이나 기타 대기 중의 오염물질로부터 태양 전지 패널을 보호해서 전지 패널의 수명을 연장시킬 뿐만 아니라, 반사율를 최소화시킨다.
- 호주 ANU :은(Ag) 나노 입자를 박막형 태양 전지에 도포해서 Plasmon 현상을 이용해서 태양 전지의 효율을 30%향상시켰다.
- 중국 Suntech : 단층의 SiNx 반사방지막과 표면 조직화를 통해서 반사율를 낮출 뿐 아니라 제조 공정을 단순화하고 제조 비용을 절감시켰다.<9월호에 이어서 계속>
미국, 일본, 독일 등은 1970년대 후반부터 정부 주도로 체계적이고 집중적인 연구개발을 통해 태양 전지 기술의 우위를 차지하고 있다. 2000년대 후반에 시장에 진입한 중국 태양광 기업들은 탁월한 가격 경쟁력을 바탕으로 전 세계 태양광 패널수요의 50% 이상을 생산하고 있다.
우리나라에서는 2005년부터 이 분야의 중요성을 인식하여 산업자원부 주도로 기술개발에 착수하였다. 그렇지만 아직까지 기술에서는 미국 기업들에, 가격에서는 중국 기업들에 밀리는 있는 실정이다. 전 세계 태양 전지 시장은 2000년 이후 높은 성장률을 보이며 고속성장하였다. 특히 2008년도의 폭발적인 수요 증가와 2010년도의 큰 시장 확대를 통해 환경친화적인 에너지 산업으로 자리매김을 하였다. 그렇지만 최근의 유럽발 경제위기로 인해서 정부의 지원이 감소하면서, 세계적으로 전체적인 수요가 감소하고 있는 추세이다. 이러한 때일수록 기술 개발에 의한 태양 전지의 발전 수율 향상이 절실히 필요하다.
태양 전지를 보호하는 커버 글라스(cover glass)에 반사 방지막(antireflective layer)을 형성시키면 유리면에서 반사되는 태양광을 이용할 수 있으므로, 태양 전지의 발전 수율을 향상시키고 발전량을 증가시킬 수 있다. 이 글에서는 이러한 반사 방지막의 기술 동향을 조사하고자 한다. 우선 태양 전지의 기본적인 작동 원리 및 종류, 그리고 최근의 기술 동향에 대해 먼저 파악하고자 한다. 이를 바탕으로 태양 전지에 사용되는 반사 반지막의 원리 및 종류, 재료에 대해서 조사하도록 하겠다. 마지막으로 태양 전지에 적용되는 반사 방지막의 최근의 기술 동향을 파악한다.
글: 정태희(NIST 객원연구원)
자료 협조: KOSEN(한민족과학기술자 네트워크) / www.kosen21.org
태양 전지의 적용되는 반사 방지막의 원리와 기술동향
반사 방지 코팅(Antireflective coating)이란 일반적으로 렌즈에 적용되는 코팅으로 가시광선 영역의 파장 대역에서 반사율을 최소로 낮추어 투과성능을 높이는 목적의 코팅이다. 일반적으로 MgF2를 이용하는 단층 코팅(single layer coating)인 경우 평균 1.5%의 반사율까지 가능하다. 더 낮은 반사율이 요구된다면 다층 코팅(multi layer coating)이 필요한데, 이 경우의 표면 평균 반사율은 0.5% 미만이 된다.
일반적으로 기판에 고굴절 재료와 저굴절 재료를 번갈아 반복해서 입힘으로써 반사율을 낮춘다. 일반적으로 400nm~700nm의 가시광선 영역에서 반사율 1% 이하, 420nm~660nm에서 반사율이 0.5% 이하로 설계하는 것이 보편적이다. 하나 이상의 반사 방지막 층을 이용하면, 좀 더 넓은 범위의 파장 대역에서 반사율을 낮추는 것이 가능하다. 그렇지만 이 경우에 제조 단가가 상승한다.
태양전지의 변환 효율을 낮추는 요인으로는 다음과 같은 손실들을 열거할 수 있다. 즉, 투과 손실, 양자 손실, 전자-정공의 재결합 손실, 불완전한 P-N 접합에 의한 손실, 태양 전지 표면의 반사손실, 전류 전압 특성에 기인하는 손실 등이다. 변환 효율을 향상시키기 위해서는 이러한 손실들이 태양전지의 어느 부분에서 일어나는지 조사하여, 태양전지의 구조설계와 공정개선을 통 해 손실을 최소화해야 한다.
이러한 손실 중에 광학적 손실은 태양 전지 표면에서 빛이 반사되거나 또는 태양 전지내부로 빛이 흡수되지 않기 때문에 일어난다. 광학 손실을 최소화하기 위한 방법으로는 전면에 입사한 빛의 반사에 의한 손실을 막는 방법과 후면에 빛을 반사하여 재흡수하는 방법이 있다[7].
전면에서의 반사 손실을 막기 위해서는 투명 전극의 표면 조직화(texturing)와 반사 방지막 코팅이 이용되고, 후면에서의 반사를 위해서는 후면 전극의 표면 조직화와 다층구조의 높은 반사율을 갖는 반사막을 이용한다. 표면 조직화의 경우에는 반복적인 형상의 크기를 제어하고 재현성 있게 구현하는 기술이 요구되며, 반사 방지막의 경우에는 정확한 굴절률과 두께의 제어가 필요하다. 이러한 기술들은 에칭과 공정 기술에 의해서 영향을 받는다.
태양 전지에 가장 많이 사용되는 실리콘은 긴 파장(1100nm)에서 34%, 짧은 파장(400nm)에서 54%의 빛이 반사로 손실된다. 그렇지만, 여기에 반사 방지막을 단층으로 입힐 경우에 이 파장 범위에서 평균 10%로 반사율을 줄일 수 있고 두 층으로 입힐 경우에는 평균 3%까지 반사율을 줄일 수 있다. 반사 방지막은 빛의 반사율을 줄이는 외에 전지의 표면을 비활성화(passivation)하여 공기로부터 전지 표면이 부식하는 것을 보호하는 역할도 한다. 태양 전지의 반사율을 줄이기 위해서 최근에는 표면을 조직화하는 방법과 반사 방지막을 코팅하는 기술을 동시에 사용하고 있으며, 이 경우에 단층의 반사 방지막을 사용하더라도 반사율을 3%이하로 낮출 수 있다.
태양 전지에서의 광이용률을 향상시키기 위해서는 투명 전극의 투과율을 높이고 반사율을 높이기 위한 표면 조직화 기술이나 후면 반사막의 반사율을 높이는 기술도 중요하지만, 이 글의 범위 밖이므로 여기에서는 다루지 않겠다. 본 보고서에서는 반사 방지막을 이용해서 투과율을 높이고 반사율을 낮추는 방법에 대해 살펴보도록 하겠다.
빛의 반사를 줄이는 방법으로 반사 방지 코팅 방법 외에도 표면 조직화(texturing)를 만드는 방법과 다공성 실리콘을 이용하는 방법도 있다. 최근에는 태양 전지의 효율을 높이기 위해서 반사 방지막 코팅과 함께 조직화도 함께 사용하기도 한다. 그러므로 조직화나 다공성 실리콘을 이용해서 반사율을 낮추는 방법에 대해서도 대략적으로 소개하도록 하겠다. 이 글에서는 반사 방지막이 태양 전지에서 반사율을 줄여주는 원리 및 이를 통한 반사 방지막의 설계방법을 먼저 기술하고, 반사 방지막으로 주로 사용되는 물질들과 그 제조 방법에 대해서도 논의하도록 하겠다.
태양 전지용 반사 방지막의 원리
반사 방지막이란 빛이 굴절률이 서로 다른 두 매질 사이의 계면에서 반사되지 않고 투과 또는 흡수되도록 돕는 막을 말한다. 이것은 렌즈나 프리즘 등에서 표면 반사를 작게 해서 투과되는 빛의 세기를 증가시키고, 반사로 인한 산란광을 제거하려는 목적으로 사용되고 있다. 태양 전지에 적용되는 반사 방지막의 원리는 태양 전지 표면(반사 방지막 윗면)에서 반사된 빛과 태양 전지 표면(반사 방지막 바닥면)에서 반사된 빛이 서로 상쇄간섭(destructive interference)을 일으키도록 하는 것이다. 이러한 상쇄 간섭을 일으키기 위한 조건은 이 두 가지 반사된 빛들의 경로차가 빛의 파장의 절반이 되게 하여 빛의 위상차가 180°가 되게 하는 것이다. 이러한 상쇄 조건을 만족시키기 위해서 반사 방지막의 두께와 굴절률의 값을 조절해야 한다. 빛의 간섭 및 상쇄 현상은 태양 전지의 반사 방지막 설계에 있어 가장 기본이 되므로 이에 대해서 좀 더 상세하게 기술하겠다.
빛은 전자기파로서 파동(wave)으로서의 성질을 지니며 정현파(sinusoidal wave)로 나타낼 수 있으므로, 같은 주파수와 파장을 가지는 파들의 겹침에 대해 수학적으로 기술하면 다음과 같다[8].
같은 주파수와 속도를 가지는 두 가지 파들은 다음과 같은 식으로 나타낼 수 있다.
E1 = E01sin(ωt + φ1) (1)
E2 = E02sin(ωt + φ2) (2)
여기에서 E는 파의 세기(amplitude)이고, ω는 각주파수(angular frequency, 2πf)이고, 여기서 f는 주파수이다. 그리고 φ는 위상(phase)이다. 이 두 파들이 공간(space)상에서 서로 공존한다고 하면 다음과 같이 이 두 파들 간의 선형적인 합(superposition)을 표현하는 것이 가능하다.
E = E1+E2 (3)
식 (3)을 확장하면 다음과 같은 식이 된다.
E=E01(sinωt cosα1+cosωt cosα1)+
E02(sinωt cosα2+cosωt cosα2) (4)
식(4)는 다시 다음과 같은 식으로 단순화될 수 있다.
E = E0sin(ωt + φ) (5)
여기에서 E0와 φ는 다음 식으로 표현된다.

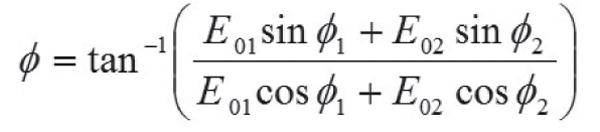
식 (5)에서 보듯, 서로 같은 주파수를 갖는 두 파의 겹침은 같은 주파수를 갖지만, 다른 세기와 위상을 갖는 파를 만들게 된다. 이 식에서 알 수 있듯이, 서로 같은 주파수를 갖는 두 파를 합했을 때에 새로운 주파수를 갖는 파를 얻을 수는 없다. 이것은 광자(photon)의 주파수가 에너지에 해당하고, 이는 변하지 않기 때문이다.
식(6)에서 알 수 있듯, 이 새로운 파의 세기는 단순히 두 파의 세기의 합이 아니라, 2E01E02cos(φ2-φ1)이라는 추가항을 가지게 된다. 이 추가항을 간섭(interference)항이라고 부른다. 두 간섭 파들 간의 위상 차를 δ (= φ2-φ1)라고 하면, 위상차 δ가 0, ±2π, ±4π,…가 될 때에 E0는 최대값을 갖게 되고, δ가 ±π, ±3π,…가 될 때에 E0는 최소값을 갖게 된다. δ가 0, ±2π, ±4π,…일 때는 두 파가 in-phase라고 하고 두 파는 서로 보강간섭을 하게 되어 세기가 커지게 된다.
반면, δ가 ±π, ±3π,…일 때는 두 파가 180°의 위상차를 가지는 것으로 out-of-phase라고 하고, 두 파는 서로 상쇄간섭을 하게 되어 세기가 감소된다. 만약 두 파의 세기가 같은 경우(E01=E02)에, 두 파가 in-phase인 경우에 두 파는 서로 보강간섭하여 초기 세기의 두 배(E0=2E01)가 되지만, out-of-phase인 경우에는 두 파는 서로 상쇄되어 없어진다(E0=0).
이러한 위상 차는 그림 1에서 보이듯이 두 파가 매질에 입사하기 전에는 동일한 위상각을 갖지만 매질 표면에서 반사될 때에는 서로 다른 경로를 여행하기 때문에 발생할 수 있다. 두 반사파 간의 위상차, δ를 수학적으로 나타내면 다음과 같다.
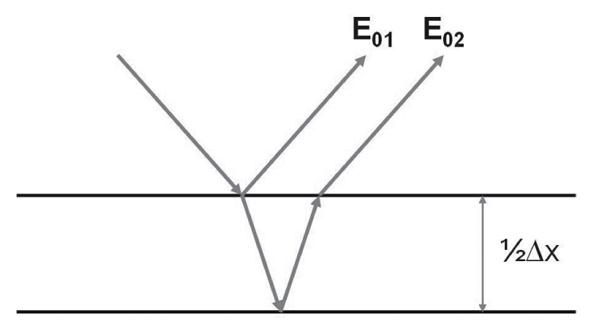
그림 1. 두 반사파들간의 간섭
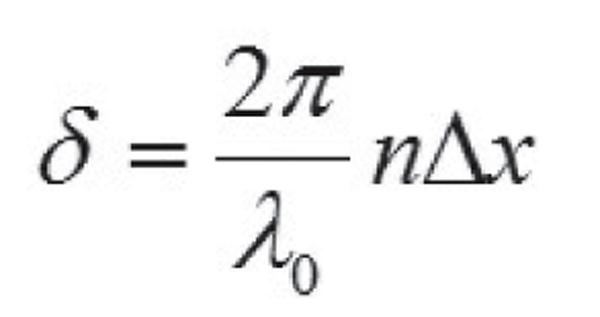
여기에서 λ0는 진공에서의 빛의 파장이고, n는 두 파가 통과하는 매질의 굴절률이고, Δx는 두 파간의 경로차이다. 이러한 경로차는 식 (8)로 부터 다음과 같이 표현할 수 있다.
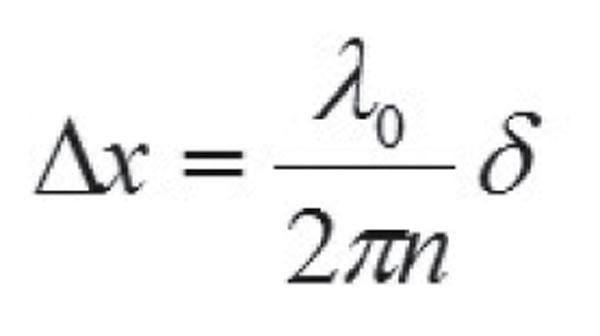
빛이 단층막 표면을 수직으로 조사하는 경우를 가정하면, 경로차 Δx는 막의 두께의 두 배가 된다. 앞에서 기술했듯이 두 파가 서로 상쇄간섭되는 조건은 위상차 δ가 ±π, ±3π,…가 되는 것이다. 따라서 막의 두께가 λ0/4n의 홀수배가 되는 경우에 반사파들은 서로 상쇄간섭되어 없어진다.
이제 빛이 반사 방지막의 표면에서 반사되는 경우에 대해서 기술하겠다[8].
빛이 서로 다른 매질 간의 경계를 수직으로 입사할 때에 그 경계면에서의 반사율는 다음과 같이 표현할 수 있다.
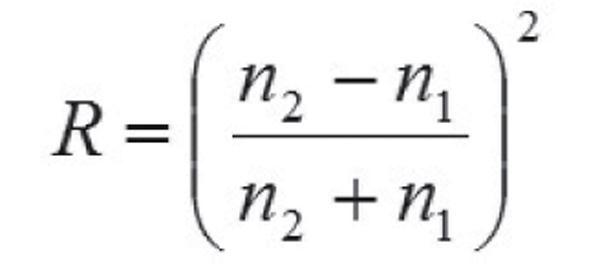
여기서 n1, n2는 각각 입사 및 투과 매질의 굴절률이다. 그렇지만 이 식은 반사 방지막 표면에서만의 반사율을 고려했다.
단층 반사 방지막이 태양 전지위에 코팅되어 있는 경우를 고려하면, 반사 방지막의 두께가 λ0/4n의 홀수배가 되었을 때에 반사율은 다음과 같이 나타낼 수 있다[8].
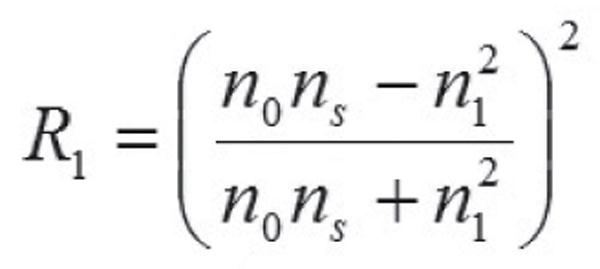
여기에서 n0는 공기중(또는 반사 방지막 위의 유리보호막)의 굴절률, n1는 반사 방지막, ns는 태양 전지(예를 들어 실리콘)의 굴절률이다.
이때에 반사 방지막의 굴절률을 다음과 같은 관계식을 갖도록 설계한다면, 식 (11)에서 알 수 있듯이 반사율은 제로가 된다.
n2, =n0ns (12)
위 수식에서 알 수 있듯이 반사 방지막의 굴절률이 반사 방지막의 위아래에 있는 물질들의 굴절률의 기하평균값(식 12 참조)이 되며, 반사 방지막의 두께가 λ0/4n1의 홀수배가 되도록 하면 반사율는 제로가 된다. 그렇지만, 이것은 입사되는 빛이 단일 파장을 갖고 있을 경우을 가정한 것이다.
실제로, 태양 빛의 경우는 그림 2에서 나타낸 것이 같이 광범위한 범위의 파장을 갖는다. 태양 빛중 파장이 600nm일 때에 태양 빛의 세기가 제일 강하므로, 파장이 600nm인 빛에 대해서 고려해 보면, 이 파장에 대한 실리콘의 굴절률은 대략 3.8이므로 공기(n0=1) 중에서 실리콘 태양 전지의 경우 반사 방지막의 굴절률 값은 1.9가 적합하다. 유리(n0=1.5)로 태양 전지의 표면을 코팅한 경우에는 반사 방지막으로 적당한 굴절률 값은 2.3이 된다.
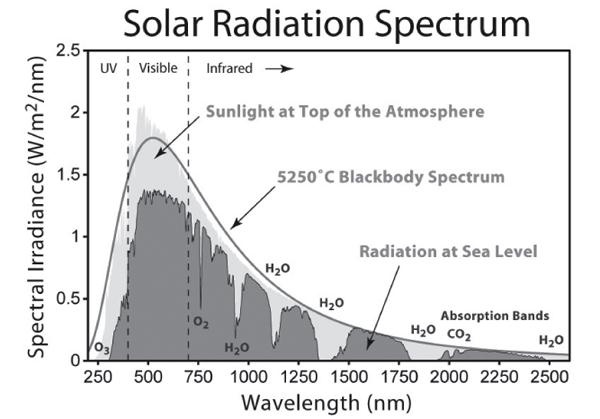
그림 2. 태양 광 스펙트럼 [9]
실제로는 태양 빛이 그림 3-3에 나타냈듯이 광범위한 범위의 파장을 갖기 때문에 반사 방지막의 두께를 λ0/4n1의 홀수배가 되는 조건을 정확하게 만족시키도록 설계할 수는 없다. 또한 그림 3에서 나타냈듯이 태양 전지의 재료인 실리콘, 반사 방지막으로 쓰이는 TiO2, 태양 전지의 커버 물질인 SiO2 등 대부분의 물질들의 굴절률 또한 파장에 따라 변화한다. 따라서 반사 방지막의 굴절률을 모든 파장 범위에서 식 (12)의 조건을 만족시키도록 설계하는 것은 매우 어렵다. 현실적으로 단층 반사 방지막을 사용하는 경우에 얻을 수 있는 최소 반사율는 10% 정도인 것으로 알려져 있다.
서로 다른 굴절률을 가진 반사 방지막을 이중으로 입히면 더욱 넓은 파장 범위에서 반사율를 감소시킬 수 있다. 반사 방지막으로 단층막이 아닌 이중막을 사용하고, 그 두께를 λ0/4n의 홀수배가 되도록 설계하는 경우에 반사율는 다음과 같이 나타낼 수 있다[8].
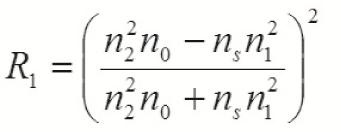
이 경우에 반사율이 제로가 되는 조건은 다음과 같다.
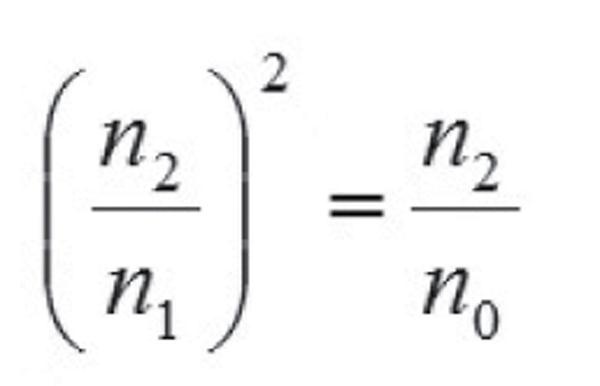
여기에서 n0는 반사 방지막 위의 매질(일반적으로 공기 또는 유리)의 굴절률이고, n1, n2는 이중 반사막의 굴절률이고, ns는 태양 전지 물질(일반적으로 실리콘)의 굴절률이다.
식 (14)의 조건을 만족하는 이중 반사막 중 첫 번째 층의 굴절률은 1.3~1.6, 두 번째 층의 굴절률은 2.2~2.6이 된다. 이중 반사막을 사용하면 좀더 넓은 파장 범위에서 낮은 반사율를 얻을 수 있다. 그렇지만 이중 반사막은 단층 반사막에 비해서 제조 단가가 상승하는 문제점을 가지고 있다.
반사 방지막으로 사용되는 물질을 선택하는 기준은 원하는 파장 영역에서 광 흡수가 일어나지 않아야 하고, 굴절률이 태양 전지에 사용되는 물질의 굴절률을 고려하여 반사율이 최소가 되도록 하는 것이다. 또한 반사 방지막을 설계할 때에는 태양광의 파장에 따른 에너지 변화(그림 2 참조), 태양 전지에 사용되는 물질들의 밴드 갭 에너지와 태양 빛의 파장에 따른 세기(그림 4 참조)와 태양 전지의 분광 반등도를 고려해야 한다. 태양 광의 스펙트럼은 일반적으로 고정되어 있지만, 태양 전지의 분광 반응도는 p-n 접합의 깊이, 도핑 농도, 표면 상태의 농도 등에 따라 달라진다.
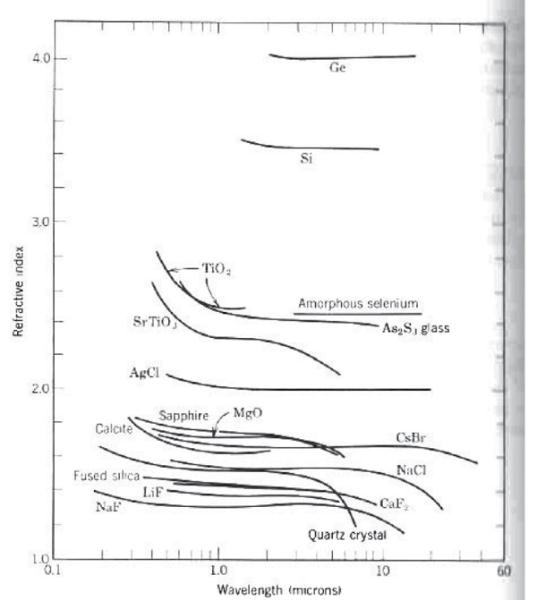
그림 3. 파장에 따른 물질의 굴절률 [10]
태양 전지의 반사율는 굴절률 외에 태양 전지의 표면 처리나 태양광의 입사각에 의해서도 영향을 받는다. 표면이 매끄럽지 못하면 표면에서 다중 반사가 일어남으로써 반사율이 감소한다. 따라서 최근의 대부분 실리콘 태양 전지는 선택적 에칭이나 광리소그래피(photolithography)방법을 통하여 표면을 조직화(texturning)한다.
또한 앞에서 기술한 굴절률에 따른 반사율 계산 수식은 태양광이 태양 전지 표면에 수직으로 입사한다고 가정하였다. 그렇지만 지표면에서 볼 때에 태양광은 시간/계절에 따라 입사각이 변하게 된다. 따라서 이것을 고려해 주어야 한다. 가능하면 태양 전지의 각도를 지표면에서 관찰할 때의 시간에 따른 태양의 위치에 따라 자동으로 변화시켜 주는 것이 최대 효율을 얻을 수 있을 것이다.
주어진 두께, 굴절률, 그리고 파장에서 반사를 제로로 줄일 수는 있지만, 굴절률은 파장에 의존하므로, 제로 반사는 오직 한 파장에서만 가능하다. 태양전지 응용을 위해서, 굴절률과 두께는 태양 전지에 사용되는 반도체 물질의 밴드갭 에너지에 해당되는 파장 및 태양 스펙트럼의 피크 파워를 고려해서 최적화시켜야 한다. 일반적으로는 파장 600nm에서 반사율이 최소화하도록 선택되는데, 이 파장이 태양 스펙트럼의 피크 파워(peak power)에 가깝기 때문이다.
반사 방지막의 재료
반사 방지막 물질은 태양 전지의 물질과 화학적인 반응을 하지 말아야 하고 전지 표면을 보호할 수 있어야 한다. 또한 오랜 시간동안 안정성이 유지되어야 하고 전지 표면과 접착성이 좋아야 하며, 수분과 온도에 대해서도 안정해야한다. 우주용으로 사용되는 전지에 있어서는 자외선(UV light)나 전하를 띤 입자들에 노출되었을 때도 안정성이 있어야 한다. 반사방지막으로서 쓰이는 재료의 굴절율을 표 1에 나타냈다.
반사 방지막으로 과거에 가장 많이 사용되던 물질은 SiO이었다[11]. 이 물질의 굴절률은 1.8~1.9로 반사율은 1% 미만으로 작기 때문이다. 그렇지만 이 물질은 가시광선 파장 영역에서 흡광 계수를 갖기 때문에 태양광을 100% 투과시키지 않고, 물질 자체에서 일부 흡수하여 이에 의한 손실이 생긴다. 따라서 이 물질은 반사 방지막으로 적합하지 않다. SiO의 대체 물질로 CeO2가 제안되었지만 제조 방법이 어렵고 굴절율이 약간 높다는 단점이 있다.
Si3N4와 Al2O3는 가시 광선 영역에서 빛을 흡수하지 않고, 굴절률이 1.8~2.0사이이므로 SiO의 대체 물질로 적합한 물질이다.
SiO2는 굴절율이 1.5로서 실리콘 표면 위에 쉽게 형성시킬 수 있고 조직화된 실리콘 표면에 적합하다. 이 물질을 사용하면 반사율을 10%에서 2%로 줄일 수 있다. BCSC(Buried Contact Solar Cell)에서 SiO2는 반사방지막 역할 뿐만 아니라 실리콘 표면의 보호막(passivation) 역할도 한다.
다결정 실리콘과 같이 조직화하기 어려운 표면이나 커버 글라스(cover glass)를 사용하는 경우는 더 큰 굴절률이 필요하다. 태양의 복사열에 의한 열화(radiation degradation)를 줄이기 위해서 사용되는 커버 글라스도 굴절률이 1.3~1.5값을 가지므로 반사율을 줄이는 역할을 한다. 커버 글라스를 사용하는 경우에 반사 방지막의 굴절률은 높은 물질을 사용해야 하는데, TiO2를 반사 방지막으로 많이 사용한다. TiO2는 물리, 화학적으로 안정하고 공기 중에서 간단하게 스프레이 방법으로 제조할 수 있다. 그렇지만, 파장 대역 400nm이하의 자외선 영역에서 빛을 흡수하는 단점이 있다.

그림 4. 태양 전지 물질들의 밴드갭과 태양 스펙트럼과의 관계
Ta2O5는 굴절률이 2.2~2.26이고 에너지 금지 대폭이 4.2eV로서 단파장에서도 투과도가 크기 때문에 Blue violet 영역의 빛에서의 반응도를 높이려는 Violet cell에 Nb2O5와 함께 사용되며, 석영(Quartz) 커버글라스(굴절률 1.5)와 함께 사용할 때 반사율을 최소로 낮출 수 있다.
실리콘 태양 전지 위의 반사 방지막 코팅을 위한 기술로써 전기화학적 에칭에 의한 다공성 실리콘(Porous silicon) 반사 방지막이 개발 중이다. 이것은 실리콘 기판위에 나노 스케일의 조직화을 형성시키는 방법으로 낮은 반사율을 가지고, 저가의 비용으로 제조가능하다.
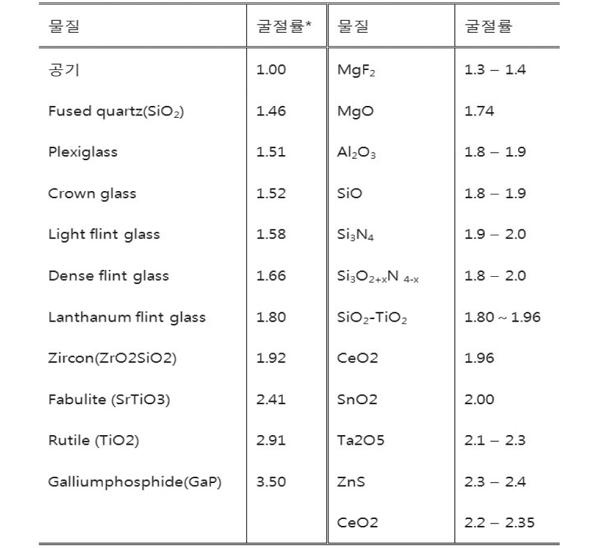
표 1. 단층 또는 이중 반사 방지막 코팅으로 사용되는 물질들의 굴절률[8, 10, 11]
태양 전지에 사용되는 반사 방지막으로서 SiO2막이 많이 이용되었으나, TiO2, CaF2/CeO2 등 여러 가지 막들이 이용될 수 있다. 최근에는 반사 방지막으로써의 특성 뿐만 아니라 실리콘 표면에 존재하는 결함들을 비활성화(passivation)시키는 역할까지 동시에 할 수 있는 SiNx 막이 많이 사용되고 있다.
SiNx 막을 형성하는 가장 일반적인 방법은 플라즈마를 이용한 화학 증착법으로서 플라즈마 내에서 분해되는 암모니아 가스로부터 질소가 공급되는데, 이 과정에서 생성되는 많은 수소 원자들이 실리콘 표면에 존재하는 많은 결함들(defects), 예를 들면 실리콘의 끊어진 결합(dangling bond)과 결합되면서 이들 결함을 비활성화한다.
반사 방지막의 제조 방법
반사 방지막을 제조할 때에 정확한 굴절률 조절과 반사 방지막의 두께 조절, 그리고 광흡수율을 줄이는 것들이 중요하다. 반사 방지막으로서 요구되는 특성으로는 적당한 굴절률뿐만 아니라 광학적으로 투명해야 한다. 결정립에서의 빛의 산란을 막아 투명도를 증가시키기 위해서 비정질 형태로 막을 증착하기도 한다. 반사 방지막을 제조하는 방법으로는 스프레이, 스크린프린팅, 스핀 코팅, 딥핑(dipping, 담구는 방법), 스퍼터링, CVD(Chemical vapor deposition, 화학 기상 증착법), PVD(physical vapor deposition, 물리 기상 증착법), 전기 분해법(Anodization), 실리콘의 열 산화(thermal oxidiation)법 등이 있다[11].
진공 증착으로 제조한 박막은 일반적으로 자외선 파장에 해당하는 빛을 흡수하는 경향이 있다. 그러나 화학적으로 증착된 막이나, 증착된 막을 산화시키거나 Anodizing시켜서 제조한 박막은 Vitreous 구조(단거리 배열(short range order)을 가진 비정질)를 가지는 경향이 있으며, 자외선의 흡수가 적다.
SiO, TiO2, Ta2O5등의 투과도와 반사율은 막을 제조하는 조건에 따라서도 크게 변한다. SiO와 TiO2는 주로 진공 증착법으로 제조하며, 기판의 온도, 증착 속도, 그리고 증착할 때의 산소 분압 등에 따라서 막의 물성이 달라진다. 대체로 증착 속도는 1-5A/sec 정도로 낮게 하고 기판의 온도는 100~250° 정도로 높게 한다.
TiO2는 저렴한 비용으로 제조하기 위해서 수증기와 Tetraisoproply titanate를 공기 중에서 150°의 온도에서 반응시키면서 스프레이 코팅 방법으로 제조할 수 있다. Werner는 Titanium isopropoxide를 스프레이 증착방법으로 증착하여 전지의 효율을 42% 이상 증가시켰다. Rausch는 고순도의 Tetraisopropyl titanate(TPT)를 Precursor로 사용하여 300-500°의 Hat wall type의 수직형 로에서 LPCVD방법으로 TiO2를 아주 균일하게 제조하였다.
Durand는 TiO2를 II-VI, III-V 태양전지에 대면적으로 적용할 목적으로 Eximer laser 스퍼터링 방법으로 증착하였다. Comsat에서는 violet cell에 반사방지막으로 Ta2O5를 기상증착법으로 코팅하여 좋은 광학적 성질을 얻었다. 그러나 스퍼터링으로 제조하였을 경우에는 가시광선 영역에서 상당한 광흡수가 일어났다. InP 태양전지의 경우 액상 전해질에서 양극 산화(Anodic oxidation)는 자연 산화물을 형성하여 반사 방지막으로 사용될 수 있다.
반사 방지막 제조에 사용되는 몇 가지 증착방법들에 대해 좀 더 살펴보면 다음과 같다.
PVD 법
SiO, CeO, TiO2, SnO2, Ta2O5막이 이 방법으로 증착된다. 막의 특성은 기판 온도나 증착속도에 의해서 영향받는다. 증착 온도는 100~250℃로, 비교적 증착 속도를 줄여서 증착시키면, 투과율이 좋은 막을 얻을 수 있다. TaOx 와 MgF2를 차례로 증착하여, 2층의 반사 방지막을 제작하면, 반사 손실을 약 4%까지 감소시킬 수 있다. PVD 법을 이용하면 막의 특성이 뛰어나지만, batch식 공정이기 때문에 생산성이 떨어진다.
CVD 법
감압 CVD, 플라즈마 CVD, 상압 하에서의 스프레이 CVD 법 등이 있다. SiO2, SnO2, Si3N4 등이 감압 CVD 법으로 증착할 수 있다. SnO2는 SnCl4를 precursor로, Ar을 캐리어 가스로 해서 450℃에서 O2와 반응시켜 약 700nm의 두께로 증착한다. Si3N4는 780℃에서 증착한 후, 550℃에서 2시간의 어닐링을 하는 등 비교적 제작 온도가 높다.
플라즈마 CVD법은 감압법에 비교해서 300℃ 정도의 저온으로 증착할 수 있는 특징이 있다. 이 방법을 통해 Si3N4가 주로 제작되는데, 분해 가스 중의 수소 원자에 의해서 표면, 계면이 불활성화되어 다결정 실리콘 태양전지의 경우, 특성이 향상하는 등의 부가적인 장점이 있다.
그렇지만 CVD법도 batch식 공정이기 때문에 양산성이 뒤떨어진다. 반면에 300~400℃에서 가열한 셀 상에 SnCl4의 에틸 acetate용액을 내뿜어, 가열분해에 의해서 SnO2를 얻는 스프레이 CVD법은 제조 비용이 낮지만, 균질한 막을 재현성 있게 얻으려면 엄격한 공정관리가 필요하다.
그 밖의 방법
스핀 코팅법, 스프레이법, 딥(dip)법 등은 도포, 증착후에 열처리에 의해서 증착물을 반사 방지막으로 변환하는 방법이다. SiO2, TiO2, TiO2-SiO2 등을 스핀 코팅방법으로 반사 방지막으로 하는 것이나, 확산제의 P2O5를 TiO2 도포제와 혼합한 액을 스핀 코팅한 후에 열처리를 하여, p-n 접합을 동시에 형성하는 것이 가능하다. 이들의 방법은 연속 생산이 용이하고 제조 비용도 저렴하지만, 균질한 막을 얻기 위해서 도포액, 도포 조건의 공정관리가 중요하다.
반사 손실 감소를 위한 조직화(Texturing) 공정
태양전지의 표면에 입사되는 빛의 반사 손실을 감소시키기 위하여 가장 널리 사용되는 것이 피라미드(pyramid) 구조의 조직화이다. 조직화는 표면에 요철을 형성하여 표면에서의 빛의 다중 반사를 유도한다. 전면 조직화 뿐만 아니라 후면 조직화 구조에서는 빛이 cell 내부에서 바로 통과하는 것을 막아 태양전지의 효율을 향상시킨다.
표면 조직화의 기법으로는 일반적으로 습식 화학에칭 기법을 사용한다. 텍스처 구조는 단순한 화학적 에칭 방법으로 알칼리성(alkaline) 용액을 이용하여 쉽게 형성이 가능하고 형성 비용이 저렴하므로 태양전지의 전체적인 제작비용을 절감시킬 수 있다.
조직화는 반도체 웨이퍼(wafer)의 특성에 따라 그 형성 방법에 차이가 있다. 먼저 다결정의 경우 다결정 공정에만 사용되는 saw damage etching을 부수적으로 수행한 후 조직화를 해야 한다. 다결정 웨이퍼는 표면 결정의 방향이 일정하지 않아 형성하고자 하는 형태의 피라미드 구조로 식각하는 것이 쉽지 않다. 이에 비하여 단결정의 웨이퍼는 결정 방향(orientation)이 일정하여 조직화를 하였을 때 바로 균일한 피라미드 표면을 얻을 수 있다.
단결정 실리콘의 이방성(anisotropic) 조직화는 태양전지에서 광 반사를 효과적으로 줄이기 위한 방법으로 잘 알려져 있다. 단결정 실리콘 태양전지는 기판의 가격이 다결정 기판에 비해 비싸지만 (100)기판의 경우 피라미드 모양의 조직화 에칭이 용이하여 반사율이 낮고 기판의 품질이 좋기 때문에 효율이 높은 태양전지를 얻을 수 있다는 장점이 있다.
단결정 실리콘을 식각하기 위한 에칭 용액으로 일반적으로 NaOH 또는 KOH에 IPA(isopropylalcohol)을 첨가한 용액을 사용한다. 이들 용액은 (100)과 (111)방향에 따른 식각 속도가 다르고, 그 결과 (100)방향에 무작위(random)한 upright 피라미드를 형성한다. 조직화 후에 400~1100nm 파장 영역에서 실리콘 표면의 평균 반사율은 약 36%에서 12%까지 감소된다. 산업적인 면에서 이와 같은 무작위한 피라미드 텍스쳐리의 단점은 재현성 있는 결과를 얻기가 어렵다는 점이다.
이것은 IPA의 끓는점(~82℃)에 가까운 온도에서만 적당한 에칭 속도를 유지할 수 있는데, 조직화 공정 동안에 IPA는 증발하고, 용액의 조성이 계속 변하기 때문이다. 또한 IPA를 공정 중에 제어하거나 다시 채워넣기가 어렵다. 게다가 IPA는 초기 비용은 물론 처리 비용이 높고, 유해한 물질이다.
이러한 이유로 인해 KOH/IPA를 대체하는 방법으로 K2CO3를 적용한 조직화 방법이 있다. K2CO3 30wt% 용액에서 100℃, 30분 동안 조직화한 결과 평균 12% 정도의 반사율을 얻었다. 또한 K2CO3 보다 저렴하여 조직화 공정비용을 줄일 수 있을 것으로 기대되는 Na2CO3를 조직화에 적용하여 반사율 약 12%를 얻은 경우도 있다. Na2CO3 용액의 경우 다른 알카리 용액(alkaline solution)을 이용한 실리콘 에칭에 비해 작고 조밀하고 무작위한 피라미드 형성이 가능하기 때문에 태양전지제작을 위한 후속 공정 중에 피라미드 팁(tip)의 손상이 거의 없이 셀 제작이 가능할 것으로 생각된다.
습식 에칭법(알칼리 에칭)은 결정의 방향성이 서로 다른 다결정 실리콘에서는 사용할 수 없다는 단점이 있다. 이러한 단점을 해결하기 위하여, 다결정 실리콘에는 기계적 에칭, 반응성 이온 에칭(reactive ion etching), 산 에칭(acidic etching)법 등을 사용하여 표면을 택스쳐링 시키는 방법이 시도되고 있다. 다공성 실리콘 층은 bath안의 HF와 에탄올을 혼합한 화학 에칭용액으로 실리콘 웨이퍼와 대면 전극을 두어 전류 밀도를 가하면 실리콘 웨이퍼 표면에 나노 스케일의 조직화가 형성된다.
투과도와 반사율은 다공성 실리콘 층의 형성 변수인 다공성 실리콘의 깊이, 다공성(Porosity)이 중요하며, 주로 HF의 농도와 전류밀도에 따라서 다공성 실리콘 층의 물성이 변한다. 이 기술은 400~1100nm에서 3.4% 낮은 반사율이 보고되었으며, Marek Lipinski은 400~1000nm에서 3%보다 적은 반사율, 12%의 효율을 얻었다.
실리콘 태양 전지에서는 조직화한 표면 구조에서 단층으로 반사 방지막을 사용할 때에는 Si3N4와 SiO2가 적당하며, 이중 반사 방지막을 사용할 경우에는 실리콘 표면에서의 전하의 재결합을 줄이기 위해서 30nm이하의 얇은 산화막을 입히고, 그 위에 ZnS/MgF2층이나 SiO2/SiN층을 코팅한다. 조직화 기술로는 전체 입사된 빛의 약 10% 정도로 반사를 줄일 수가 있으며 반사 방지막 코팅을 함께 사용할 경우에 3% 정도까지 반사를 줄일 수 있다.
태양 전지에서 다공성 실리콘(Porous Si)의 역할
PECVD와 같은 고가의 진공장비를 사용하지 않고도 태양전지를 생산하기 위해, 저렴한 화학 에칭 방법으로 광흡수를 줄이기 위한 기술들이 많이 연구되고 있다. 예로 수산화나트륨(NaOH), 수산화칼륨(KOH), 이소프로필알콜(IPA) 등으로 조합된 알카라인 에칭용액을 들 수 있다.
이는 유기적인 작용제로서 단결정 실리콘의 표면 조직화에 사용된다. 하지만 결정립의 방향인 (100)으로 에칭되기 때문에 다결정 실리콘 태양전지에 적용하는 경우, 태양전지의 낮은 변환효율을 초래하게 된다. 그리고 강한 산화작용제(oxidizing agent)로 쓰이는 불산(HF)과 질산(HNO3)으로 혼합된 용액으로 에칭하는 방법이 있으나, 실리콘 표면 에칭의 균일성과 두께의 조절이 어려운 단점이 있다.
전기화학적 양극산화 방법으로 형성된 다공성 실리콘(porous silicon) 반사 방지막은 두께 및 다공성도(porosity) 조절이 가능하며, 고전류 밀도의 양극산화반응으로 다결정 실리콘의 결정립과 결정크기의 상관없이 실온에서 수십 초 내 간단하게 균일한 표면이 형성 가능하다.
다공성 실리콘(PSi)은 미세 전자 기기(microelectronics), 전자발광 소자(electroluminescent device), 각종 센서는 물론, 광방출 재료(light emitting material), 광검출기(photodetector) 등 광전자 분야로의 응용 가능성을 인정받아 개발 및 적용되고 있으며, 1960년대 후반부터 연구가 진행되고 있다.
특히 미세 전자 기기 분야에서는 다공성 실리콘을 이용한 SOI(silicon on insulator) 구조 제작에 적용하여 1970년대부터 적극 활용하고 있다. 태양전지 분야에서는 1980년대 이후로 연구가 진행되어왔다. 다공성 실리콘의 빛 트랩(light trapping)과 반사 방지 특성은 물론 제작이 쉽고, 텍스쳐를 제어할 수 있다는 점이 특히 태양 전지에 응용하기에 적합하다. 또한 막의 굴절률을 조정하여 단층 또는 다층 반사 방지막으로 사용하기 위한 연구도 진행되고 있다.
다공성 실리콘은 태양전지 구조에서 표면적 특성 때문에 반사 방지막으로써 적용된다. 이때 굴절률은 다공성도(porosity)와 그 형상(morphology)에 의존하게 되는데 빛이 표면에서 직접 반사되는 것을 막고, 또한 반사 방지막 아래에 있는 구조에 바로 입사되는 것을 막아주어 표면에서 충분히 태양에너지를 흡수할 수 있게 해준다. 반사 방지막 이외의 다공성 실리콘의 역할은 기존의 텍스쳐 구조와 표면 passivation, 그리고 선택적 에미터(selective emitter)로써의 역할도 한다.
다공성 실리콘은 빛 트랩(light trapping)과 반사 방지 특성이 있고, 제작이 쉽고, 텍스쳐를 제어할 수 있다는 장점이 있어 태양 전지에 응용하기에 적합하다. 또한 막의 굴절률(refractive index)을 조정하여 단층 또는 다층 반사 방지막으로 사용할 수 있다. 다공성 실리콘은 스크린 프린팅한 은(Ag)전극을 갖는 태양 전지의 p-n 접합(junction) 위에 형성할 수 있다. 이와 같이 다공성 실리콘 위에 선택적인 이미터(selective emitter)를 갖는 형태의 태양전지는 25㎠ 면적의 다결정 실리콘 태양전지에서 13.2%의 변환효율을 나타내었다.
초기 다공성 실리콘 개발 이후로 이에 대한 응용은 주로 미세 전자 기기(microelectronics) 및 센서 분야에 주로 적용되어 왔다. 태양전지에는 최근 양산용 저가격화 공정 개발과 함께 연구가 활발히 진행되고 있으며, 2000년대 이후 직접 전지에 적용하려는 시도가 계속되고 있다.
지금까지는 보통 적용이 간단한 화학적인 에칭(chemical etching) 방법을 사용하여 많은 실험이 진행되었으나, 막 특성을 원하는 대로 제어하기 위해서는 전기 화학 에칭(electrochemical etching) 방법이 더 바람직할 수 있다. 단층뿐만 아니라 다층막을 형성하는 것이 가능하기 때문에 제어가 가능하다면 태양전지에 적용하여 여러 가지 상승효과를 얻을 수 있을 것으로 기대된다. 특히 제조 공정 측면에서 비용절감 효과가 기대된다. 다공성 실리콘 반사 방지막은 다른 반사 방지막 코팅 기술에 비해 제조 비용을 절감할 수 있다. 이는 다공성 실리콘 방법이 SiN나 TiO2가 없이도 효율을 약 40% 향상시킬 수 있기 때문이다.
다공성 실리콘은 불산(HF, Hydrofluoric solution)에서 전기화학 에칭 (electrochemical etching)과 화학 에칭(chemical etching) 이라는 두 가지 방법으로 얻을 수 있다. 두 방법 모두 부분적인 다공성 선택적 이미터(porous selective emitter)를 갖는 새로운 타입의 태양 전지 셀(photovoltaic cell)을 제작하기 위해 사용된다.
화학 에칭법은 대량생산에 적용 가능하지만, 다공성 실리콘 형성 기구가 HF 용액의 농도, 온도, 에칭 시간에 의해 제어되는 결점이 있다. 이에 반해 전기화학 에칭법은 다공성 실리콘의 다공성을 결정하기 위한 주요 파라미터가 전류 밀도(current density)이다.
전기화학 다공성 실리콘 형성 방법은 anodization 시간이 짧기 때문에 상업적으로도 적용이 가능하다. 앞면 금속 그리드(Front metal grid)를 형성하고 다공성 실리콘를 제작하면, 짧은 공정 시간으로 인해 접촉(contact) 아래 영역의 손상을 최소화하고 그리드를 제외한 영역만 에칭되는 효과를 얻을 수 있다. 따라서 선택적인 이미터 효과 또한 얻을 수 있다. 실제로 다공성 실리콘층은 스크린 프린팅한 은전극이 형성된 결정질 실리콘 태양전지의 p-n 접합위에 형성하는 방법이 연구되고 있다.
불산이 함유된 용액에서 전기화학적 양극산화 과정으로 실리콘 기판의 실리콘 원자를 화학적으로 용해하여 다공성 실리콘을 표면에 형성하여 표면 광학적 손실을 최적화할 수 있다. 이러한 다공성 실리콘 반사 방지막은 전기화학 반응의 주요 변수들로써 실리콘의 물성적 특징을 변화시키어 광 투과도를 높일 수 있었으며, 태양전지에 사용되는 반사 방지막의 형성구조(morphology)를 제어하여 표면반사율이 최소가 될 수 있도록 제작할 수 있다.
알카리 에칭(saw damge)된 기판에 수십 초 동안 전기화학적 양극산화 과정으로 다공성 실리콘층을 형성하여 반사율을 줄였으며, 현재 상용화되고 있는 SiNx의 반사 방지막의 평균반사율 14%과 비교하여 넓은 파장 대역 400-1000nm에서 다공성 실리콘 반사 방지막의 평균 반사율 4.7%을 얻을 수 있다.
다공성 실리콘 형성층을 단층으로 형성하여 표면반사율을 2% 이하로 낮출 수 있으며, 반사율을 더 감소하기 위해서 2층(double antireflection coating layer)으로 반사방지막을 사용할 경우에는 다공성 실리콘 표면에서의 전하의 재결합을 줄이기 위해서 300A 이하의 얇은 산화막(SiO2)을 형성하여 반사율을 저감할 수도 있다. 현재 상용화되고 있는 SiNx의 단층 반사 방지막의 다결정 실리콘 태양전지의 변환효율이 12.3%인 반면에 다공성 실리콘 반사방지막을 적용한 다결정 실리콘 태양전지는 13.53%의 변환효율을 나타낸다.
최근에 태양 전지 표면의 광손실을 줄이기 위해 표면에 무작위한(random) 피라미드를 형성하고, 피라미드표면에 다공성 실리콘을 제작한 것이 보고되었다. 일반적으로 적용하는 10㎛ 이상의 크기를 갖는 피라미드와 달리 5㎛ 이하의 작고 밀도가 높은 무작위한 피라미드를 적용한 조직화로 표면 반사율을 최소 12%까지 낮출 수 있었으며,그 위에 반사 방지막 코팅 역할을 하는 다공성 실리콘을 제작함으로써 최소 약 4% 정도까지 표면 반사율을 낮추었다.
또한 400~1000nm 파장 영역에서 반사율이 고르게 낮아지는 효과를 볼 수 있었으며, 실리콘 태양전지에 일반적으로 진공장비를 사용하여 제작되는 단층 반사 방지막 코팅 막이 10% 정도, 다층 반사 방지막 코팅 막이 약 5%이하로 반사율을 낮출 수 있는 점에 비교하면 상대적으로 저렴하고 우수한 특성을 나타냄을 알 수 있었다.
태양전지에서 다공성 실리콘층은 여러 가지 역할을 할 수 있는데, 반사 방지막 코팅으로 이용하는 방법이 잘 알려져 있다. 이 밖에도표면에 요철 구조, 즉 조직화를 만들어 빛을 트랩(light trapping)하는 효과를 증대시키거나, 단일 이미터(single emitter)를 형성한 셀에서 전극 부분을 제외하고 다공성 실리콘층을 형성하여 선택적인 이미터(selective emitter)를 만드는 효과를 얻을 수 있는 등의 다양한 역할을 할 수 있다.
반사 방지막 적용 현황
MINP(Metal-Insulator-NP junction) 태양전지는 최초로 18% 이상의 변환효율을 보인 실리콘 태양전지로 반사손실을 최소화하기 위하여 ZnS와 MgF2를 이용한 이중 반사 방지막 구조를 적용하였다.
PESC(Passivated Emitter Solar Cell) 태양전지는 20%의 벽을 넘은 최초의 전지로, 여기에서는 기판 후면의 조직화로 후면에서 빛을 난반사 시켜 light trapping 효과를 주며, 이중 반사 방지막을 이용한 반사손실을 감소시켰다.
PERC(Passivated Emitter and Rear Cell) 태양전지의 변환효율은 23.3%이다. 여기에서는 열처리를 하지 않기 때문에 후면에서 실리콘과 합금을 형성하지 않은 알루미늄은 실리콘 산화막과 작용하여 후면에서의 빛 반사를 97% 이상 시킬 수 있는 반사막 역할을 하여 light trapping 효과를 향상시켰다. 전면에는 산화막의 두께를 25nm으로 줄이고 MgF2/ZnS를 이중 반사 방지막으로 사용하였다.
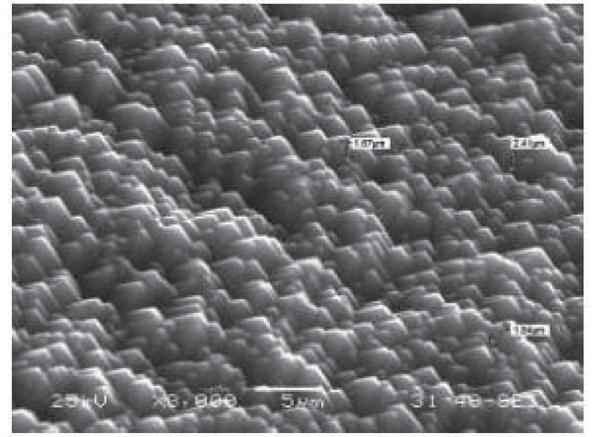
그림 5. PLUTO cell의 조직화(texturing)된 SiNx 표면
CNR(Comsat nonreflective) 전지는 실리콘 표면을 피라미드 형태로 조직화하고 그 위에 Ta2O5를 코팅하여 대부분의 유용한 파장 범위에서 반사율을 약 2% 정도로 줄였다. Rothwarf는 Cu2S/CdS 태양전지에 60nm 두께의 ZnS와 100nm 두께의 MgF2를 코팅하였다. Apfel은 실리콘에 12nm 두께의 MgF2와 6nm 두께의 ZnS를 코팅하였다.
Zhao는 PERL 태양전지에 이중 반사 방지막을 형성하기 위해서 SiO2 두께를 20nm로 줄이고, 그 위에 MgF2와 ZnS를 진공증착법으로 코팅하여 전지의 효율을 24%까지 얻었다. Peyman은 이 두 층의 반사 방지막을 다결정 실리콘 태양 전지에 적용하여 17.1%의 효율을 얻었다. SiO2/ZnS 이중 반사방지막을 PECVD 방법으로 제조하여 실리콘 태양 전지에 적용하면 MgF2/ZnS 보다 반사율과 흡수도는 약간 높지만 증착 도중에 결함(defect)이나 표면 보호(surface passivation)에 의한 개방 전압 증가로 효율이 더 증가한다고 보고되었다.
현재 상업용으로 가장 많이 적용되고 있는 태양전지는 스크린프린팅 방법으로 제작되고 있으며, 변환효율은 약 14-16% 수준이다. 여기에서 반사방지막(SiNx 혹은 TiO2)을 진공장비로 형성(PECVD,APCVD)하고 전면전극을 스크린 프린팅으로 형성을 하게 된다. 전면전극은 은이다.
현재 상업용 다결정 실리콘 태양전지의 반사 방지막으로서는 SINx가 많이 사용되고 있다. 이는 반사 방지막으로써 적절한 반사율과 표면과 벌크 페시베이션(passivation)역할, 태양전지의 결함 등을 보완할 수 있는 여러 장점이 있기 때문이다. 하지만, SiNx의 반사 방지막 형성은 PECVD(plasma enhanced chemical vapor deposition)와 같은 고가의 진공장비가 사용된다.
반사 방지막의 태양전지 적용 현황
•일본 전기 유리(Nippon Electric Glass Corporation)
일본 전기 유리는 태양광 전지의 감광 부분에 닫는 빛의 양을 극대화 시켜 효율을 개선시킬 수 있는 투명 유리를 2011년도에 개발하였다. 투명 유리란 유리에 반사 방지막을 코팅하여 반사되는 빛을 줄여서 눈에 거의 보이지 않게 만든 유리이다. 일반 유리에서는 보통 92퍼센트의 빛이 투과되고 나머지 빛은 반사된다.
이 투명 유리에서는 99.5퍼센트 가량의 빛이 투과하고, 0.5%의 빛만이 반사된다. 이 투명 유리는 휴대폰 스크린이나 태양광 전지의 패널 면에 사용될 수 있을 것으로 기대된다. 이 투명 유리에 사용된 반사 방지막은 30층 이상으로 이루어져 있고, 각 층의 두께는 수 나노미터이다.
현재의 태양광 전지에 사용되는 반사 방지막은 이 투명 유리만큼 높은 투과율을 내지는 못하고 있다. 다만, 실제로 태양광 전지에 이 반사 방지막을 사용하기 위해서는 기존의 단층이나 이층 구조의 반사 방지막에 비해서 비슷하거나 적은 제조비용이 요구되는데, 이것이 가능할지가 의심이 된다.
•Henan Succeed New Energy Material Co Ltd (일본)
일본의 Henan Succeed New Energy Material Co는 극도의 투명 유리(Ultra transparent glass)를 2011년 4회 국제 광전기 발전 컨퍼런스에서 발표하였다. 이 유리는 97퍼센트의 투과도를 가져 태양 패널에 사용되기에 적합하다. 이 유리를 사용하면 태양 전지의 효율을 2~3% 향상시킬 수 있다.
이 유리는 100nm 두께의 SiO2로 이루어진 반사 방지막으로 코팅되고, 700도에서 열처리되었다. 일반적인 유리가 전면과 후면에서 각각 4%의 빛을 반사하는 데, 이 유리는 0.5~1.5%의 빛만을 반사하므로, 전체적인 투과도는 91%에서 97%로 향상된다. 400~500nm의 파장대역에서 이 유리의 투과도는 99%이다.
•New Energy Technologies (미국)
New Energy Technologies는 투명 태양 전지 셀을 개발하였는데, 이것은 어떤 종류의 유리 위에도 스프레이 방법으로 도포될 수 있다. 이들은 태양 전지 셀에서 모든 금속들을 성공적으로 제거했고, 이것들을 환경친화적인 투명 물질들로 교체했다. 빛의 투과를 막는 금속 전극들이 사라졌으므로 태양 전지의 효율은 증가할 것이다.
이 스프레이 방법으로 만든 태양 전지셀은 비싼 실리콘 웨이퍼로 만든 기존의 태양 전지 셀에 비해서 저렴하다. 또한 고진공과 고온 열처리가 필요한 박막형 태양 전지에 비해서 빠른 생산이 가능하다. 또한 이 태양 전지셀은 직접적인 태양광뿐만 아니라 형광에 의해서도 전기를 생산할 수 있다. 이것을 일반 상업용 빌딩이나 가정집에 적용할 수 있을 것으로 전망했다.
•3M (미국)
3M에서는 태양 전지 패널에 사용될 수 있는 새로운 플라스틱 박막을 개발했다. 이 박막은 다층막(multilayer)의 fluoropolymer을 기반으로 한 시트로, 태양 전지 패널에 직접적으로 붙일 수 있다. 이 박막은 수분이나 기타 대기 중의 오염물질들로부터 태양 전지 패널을 보호해서 전지 패널의 수명을 연장시킨다.
이 플라스틱 시트는 CIGS(copper-indium-gallium-selenium) 태양 전지 셀에 적용될 수 있을 것으로 여겨진다. CIGS 태양 전지 셀은 수분에 노출되면 노화가 일어나서 수명이 단축된다. 태양 전지에 사용되는 유리의 일반적인 두께가 3000μm인데 비해서, 3M의 플라스틱 막의 두께는 23μm으로 매우 얇다.
이 물질은 자외선, 고온, 수분에 강하다. 또한 반사율이 최소가 되도록 설계되어 태양 전지의 효율을 향상시킬 수 있다. 이 박막은 하루에 50μg의 수분만을 통과시키는데, 이것은 다른 박막들에 비해서 수백 배 적은 것이다. 더욱이 박막을 태양 전지 패널에 직접 붙일 수 있기 때문에 제조 단가도 저렴하다.
•Plasmonic Thin film solar cells by Australian National University in Canberra
호주 국립 대학교의 Kylie Catchpole는 박막형 태양 전지의 표면에 은(Ag) 나노 입자들을 도포시키는 것을 연구하고 있다. 이 경우 입사 광은 반사되지 않고, 굴절이 되어서 태양 전지 셀안에서 앞뒤로 되 튄다(bounce back and forth). 이를 통해서 긴 파장의 빛들이 흡수될 수 있게 한다. 이것은 금속 나노 구조의 Plasmons 현상을 이용한 것이다. 이러한 Plasmon 현상을 이용한 CdTe박막형 태양 전지는 기존의 태양 전지에 비해서 30%의 효율 향상을 나타냈다.
•Sixtron Advanced Materials (미국)
Sixtron Advanced Materials은 태양 전지의 태양 광에 의한 열화를 방지해주는 Silexium 박막을 개발했다. 다결정 실리콘 태양 전지는 일반적으로 붕소(Boron) 도핑되는데, 이 때에 산소도 같이 포함된다. 태양 광선이 실리콘 웨이퍼에 조사될 때에 산소와 붕소는 서로 결합(산화)되어(light induced degradation) 셀의 효율을 3-5% 감소시킨다. 카본이 포함되어 있는 Silexium 박막을 코팅하면, 카본이 산소와 먼저 결합하기 때문에 붕소가 산소와 결합하는 것을 막는다.
•Suntech (중국)
Suntech는 PERL(Passivated Emitter and Rear Locally diffused) 셀에서 적용되었던 SiO₂/ZnS/MgF₂으로 구성된 이중 반사 방지막 코팅(Double Layer AntiReflection coating) PLUTO cell에서는 저가의 공정을 위해 SiNx의 단층 반사 방지막(Single Layer AntiReflection coating)으로 변경하였다. 이 때문에 반사율이 약간 증가하였다.
기존 PERL 셀은 역피라미드 형태의 조직화(Texturing)를 위해서 마스크를 사용하는 광리소그래피(Photolithography) 공정을 적용하기 때문에 복잡해진 공정으로 인해서 제조 비용이 높은 문제점이 있었다. PLUTO 셀은 전통적인 조직화(Texturing) 공정을 적용하여 수직의 피라미드 형태를 제작함으로써 역피라미드 형태에서 생성된 피라미드 간의 평평한 면을 제거해주어 빛의 반사율을 줄여주었고, 이는 단층 반사 방지막으로 인해서 증가된 반사율로 인한 손실률을 감소시켜주는 역할을 해주고 있다. 그림은 조직화된 SiNx 반사 방지막의 표면사진이다.
•신성솔라에너지 (한국)
기존 태양전지 제조과정에서 반사 방지막 형성을 위해 SiNx공정을 단층으로 형성했으나, 신성솔라에너지에서는 SiNx 대신 이중 반사방지막을 형성해 태양전지 표면에서의 빛의 반사율을 더욱 떨어뜨렸다. 또한 태양전지의 표면 구조 개선을 위해, 기존의 습식화학식 조직화(Wet chemical texturing) 방법 대신에 심도반응성 이온 에칭(Deep Reactive Ion Etching) 방법을 이용하여 기판 표면상에 나노팁을 형성하여 태양전지 표면 반사율을 낮게 했다.
사업 결과의 활용
·수집된 반사 방지막의 주요 정보는 현재 기술 개발 및 생산 중인 기업과 연구 기관에 전달.
·태양 전지 반사 방지막의 제조 공정이 구체적으로 조사되면 다양한 공정의 기술 개발에 소요되는 장비 개발의 투자 소요 대폭 감소.
·차세대 핵심 기술 개발 아이템 및 핵심 이슈의 분석을 통하여 선진국과 기술격차 해소에 필요한 시간 대폭 단축, 우위를 점할 수 있는 기술 개발에 집중 가능.
·수집된 정보를 활용해서 기술 세미나나 기술 교육을 실시할 수 있음.
회원가입 후 이용바랍니다.
개의 댓글
댓글 정렬
BEST댓글
BEST 댓글
답글과 추천수를 합산하여 자동으로 노출됩니다.
댓글삭제
삭제한 댓글은 다시 복구할 수 없습니다.
그래도 삭제하시겠습니까?
그래도 삭제하시겠습니까?
댓글수정
댓글 수정은 작성 후 1분내에만 가능합니다.
내 댓글 모음