차세대 비실리콘계 나노박막 태양전지 원천소재 및 소자 기술
차세대 비실리콘계 나노박막 태양전지 원천소재 및 소자 기술
2004년 향후 50년간 인간의 10대 문제점 중 에너지 문제가 1위로 보고되고 있다. 독일의 기후변화협의회에 따르면 태양에너지의 이용 가능량은 전세계 연간 에너지 소비량의 약 2,859배에 이르는 것으로 조사되었으며, 이는 풍력 및 바이오매스가 각각 200배, 20배 정도의 규모인 것에 비해 무한정의 양을 보유하고 있는 것으로 분석된다.
2012년 이후 Kyoto Protocol의 2차 의무 대상국으로 선정이 유력한 국내의 경우에도 온실 가스 감축 의무가 본격화될 것으로 예상됨에 따라 온실가스 배출 등의 환경저해 요인이 전혀 없는 친환경에너지로서 태양광에너지의 수요가 증가할 것으로 예상된다.
태양광에너지는 국내에서도 무한정 자체 조달이 가능하여 석유나 천연가스처럼 수입에 의존하지 않아도 되며 입지조건에 크게 영향을 받지 않아 지역 및 규모에 상관없이 설치가 가능하고 기술개발로 설치비용이 절감될 경우 유지비용이 타 에너지원 대비 낮은 수준이라는 장점을 갖고 있다.
글: 연구책임자 김환규 교수 외
고려대학교 신소재화학과 / www.korea.ac.kr
자료제공: KOSEN(한민족과학 기술자 네트워크)
www.kosen21.org
사업의 목적 및 필요성
OECD 국가들의 에너지원별 이용률을 살펴보면 화석연료, 수력 등의 비중이 줄어드는 반면 신재생에너지가 차지하는 비중은 지속적으로 증가하는 추세이다. 이는 초기 투자비용이 과다하게 소요됨에도 불구하고 신재생에너지가 화석에너지의 고갈 문제와 환경문제에 대한 유일한 해결방안이라는 관점에서 각 선진국은 정부 주도하에 신재생에너지에 대한 과감한 연구개발 및 보급정책을 추진해 오고 있다.
태양전지는 태양광발전의 핵심기술로 태양전지 및 관련 시장이 전체 태양광발전 시장의 35%를 차지한다. 전세계 태양광 산업은 1999년 2006년까지 연평균 약 40% 이상의 성장률을 나타내면서 급격한 속도로 성장, 2007년 기준 세계 태양전지 시장은 약 60억 달러에 이르는 것으로 추정된다.
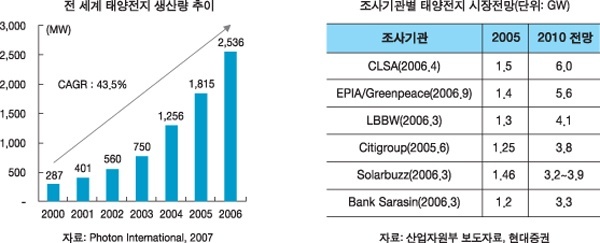
태양광 산업의 성장에 따라 핵심기술인 태양전지 산업도 크게 성장하여 1999년 287MW에 불과하던 생산량이 2006년에는 연평균 43.5% 성장하여 2,536MW를 기록했다. 2010년 태양전지 시장규모에 대한 전망은 관련 업체나 조사기관마다 큰 편차를 보이지만 시장 전망치는 최근 상향 조정되는 추세를 보이고 있다.
Photon International은 2006년에는 2010년 태양광 발전 규모를 10GW 수준으로 예상하였으나 최근 발표에서는 전망치를 14GW로 상향조정하였으며, CLSA(Credit Lyonnais Securities Asia)의 경우 2004년 예상치 5.2GW를 2005년 6GW로 상향한 이후 2006년 4월에는 다시 10GW로 상향 조정하였다.
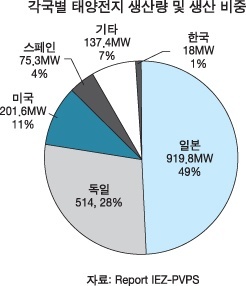
일본, 유럽, 미국이 전세계 태양전지 시장을 주도하고 있으며 이들 국가 생산량이 약 90%에 이르는 것으로 나타났다. 최근 중국, 대만, 필리핀은 최근 2년간 최고의 성장률을 나타내면서 기존 기술 보유국의 위치를 위협하고 있으며 특히 중국은 최대 생산국인 일본과 독일을 머지않아 따라 잡을 것으로 예상된다.
태양전지는 면적에 의해 발전량은 변하지만 발전효율은 규모에 관계없이 일정하기 때문에 소규모에서 대규모 부하까지 가능하다. 발전을 위한 연료공급의 필요가 없는 것은 물론이고 기계적인 구동장치가 없어 보수가 필요 없다.
태양광발전은 2000년대 이후 연평균 38%의 설치 증가율을 보이면서 타 신재생에너지(풍력 28%, 바이오매스 3.5%, 지열 3.0%) 대비 가파른 성장세를 보인다. 또한 전 세계 태양광발전 규모는 1999년 202MWp 규모에서 연평균 40% 성장하여 2006년에는 2,204MWp 수준에 도달하였으며 중장기적으로도 태양광발전의 성장 추세는 지속될 것으로 예상된다.
유럽신재생에너지협회에 따르면, 현재 태양광에너지의 사용비중은 전체 신재생에너지 중 0.1% 수준에 불과하나, 향후 고성장세를 지속하여 2040년경에는 전체 에너지 대비 약 25%, 신재생에너지 대비 30% 이상을 점유할 것으로 분석된다.
에너지 부존자원이 거의 없는 국내 현실에서 기존 주택이나 건물의 지붕 및 벽면에 태양전지를 설치할 경우 태양광발전으로 약 19GW의 발전설비를 구축할 수 있어, 이는 2002년 국내발전량이 306,474 GWh의 4.5%에 달하며, 앞으로 신축 주택이나 건물을 감안할 경우 그 기여도는 더욱 증대될 것으로 사료된다.
국내 보급시장은 세계 평균을 크게 상회하는 급속한 성장세를 보여 2004년 2.6MW, 2005년 5MW, 2006년 22MW, 2007년 44MW, 2008년에 100MW으로 예상됨에 따라 2020년 국내 보급규모는 4GW, 2030년 18GW, 수출규모는 2020년 연간 1조 4천억 원에서 2030년 6조원에 이를 것으로 전망된다. 신재생에너지의 총 발전량 중에서 태양광에너지의 비중은 1998년 이후 연평균 약 0.067%로 여전히 낮은 편이나, 자가용을 중심으로 매년 증가하고 있어 2006년에는 신재생에너지 전 체 발전량 중 0.15%의 비중으로 크게 상승하고 있다.
특히 정부가 태양광에너지 지원 사업을 시작한 2004년을 기점으로 보급량이 급격한 증가 추세를 보이고 있으며, 2006년 사업용 태양광발전 보급량이 급상승하여 상대적으로 가정용 분야와 균형을 이루어 가고 있다.
1991년 스위스 Gratzel 교수에 의하여 소개된 염료감응 태양전지는 비록 짧은 기간이지만 11% 이상의 높은 변환효율을 구현하였으며 모듈화에 대한 기술이 진척되면 상품화가 2~4년 이내에 이루어 질 전망이다. 또한 제작과정이 간편하고 가격이 저렴하여 기존 실리콘 태양전지에 버금가는 차세대 태양전지로 부각된다.
전해질이 고체화되고 효율이 6~7% 정도가 될 경우 제품이 flexible하여 손으로 가지고 다닐 수 있는 mobile phone, PC, 내구용 및 가구류 등의 축전용으로 사용할 수 있는 미래 첨단형 기술이다.
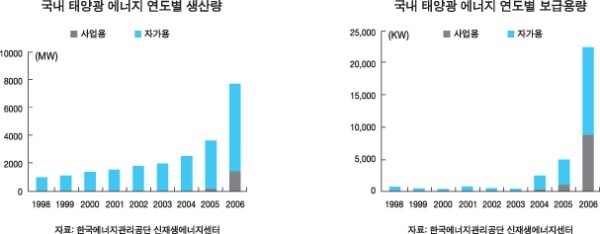
I-III-VI2 족 chalcopyrite 계인 Cu(In,Ga)Se2(CIGS) 화합물 반도체는 직접적인 광전이가 이루어지는 밴드 구조를 가지고 있어 광 흡수율이 큰 장점이 있다. 특히, CIGS 박막 태양전지는 19.9% 셀 효율(NREL, 미국)을 보이고 있으며, 이는 다결정 실리콘 태양전지와 대등한 수준임(20.3%). 따라서, 향후 태양전지 시장에서 실리콘보다 저렴하고 대면적화가 가능한 CIGS 막 태양전지 기술의 약진이 예상된다.
집광형 III-V 화합물 반도체 태양전지는 태양전지 제조, 광학계 설계, tracker 등 다양한 산업과 다양한 재료를 필요로 하여 집광형 태양광 발전 시스템 분야를 육성함으로써 다양한 산업이 동시에 육성 가능하다. 따라서 과학기술의 급격한 발전과 더불어 연구자, 기술자에게 있어 관련 해외 최신정보의 입수는 업무의 중요한 한 부분으로 인식되고 있으며, 효율적 정보 입수의 여부에 따라 연구개발 성과에 큰 차이를 보이고 있다.
정책입안자의 입장에서도 국가 미래발전을 위한 핵심원천기술을 대상으로 세계에서 가장 앞서 가는 국가의 정책 및 연구개발 동향을 파악하고 전략적 협력을 모색하는 것이 매우 중요한 업무로 되고 있다. 특히, 입수된 해외기술정보를 국내 연구자, 기술자, 정책결정자들에게 빠르고, 편리하게 확산시키는 일은 정보획득 업무만큼이나 중요해 지고 있다. 선진 외국은 과학기술정보가 창출하는 부가가치의 중요성을 먼저 깨닫고, 이미 다양한 매체로 발생하는 과학기술정보를 인터넷을 통해 자국의 관계자들에게 정보를 확산시키는데 노력하고 있다.
사업의 내용 및 범위
'나노기술'을 통해 물질이 가지고 있는 특성을 변환시킴으로써 기존의 물성 한계를 극복하여 나노 박막태양전지용 원천 소재 개발기술로서의 일본, 미국 및 유럽 기술 동향을 조사했다.
미국 나노 박막태양전지용 원천 소재 기술의 신재생 에너지 기술로서 활용하고 있는 Project 책임자 면담(NREL)을 통한 기술 동향 조사 및 현재 기획중인 특정 Program 상세 정보를 조사했다.
미국 유기 태양전지 원천 기술의 신재생 에너지 기술로서 활용하고 있는 유기 태양전지 발명자인 A. J. Heeger 교수 면담을 통한 기술 동향 조사 및 현재 기획중인 특정 Program 상세 정보 조사했다.
독일 HMI(Helmholtz Centre Berlin for Materials and Energy) 연구소 신재생 에너지 기술(CIGS)에 대한 기획 및 Project 담당자 면담을 통한 기술 동향 조사했다.
스위스 연방공대 염료감응형 태양전지 발명자인 M. Graetzel 교수 국내 초청을 통한 스위스 전반 신재생 에너지 기술 동향 조사 및 기획 방향 조사했다.
일본 AIST 연구소 신재생 에너지 기술에 대한 기획 및 Project 담당자 면담을 통한 기술 동향 조사했다.
정보조사 결과
국외 현황
1991년 스위스연방공대 Gratzel 교수팀이 다공성 나노 TiO2와 류테늄 염료를 이용한 염료감응 태양전지를 최초로 개발(Nature 1991, 353, 737)했다. 그 이후로 다양한 염료개발, 유기 정공전도체를 이용한 고체형 염료 광전지 개발(Nature 1998, 395, 583), gelling 화제와 plasticizer 화제를 이용한 반고체전해질 개발(JACS, 2004, 13590; J. Mater. Chem. 2004, 14, 1905)및 나노입자를 이용한 겔화 전해질(JACS, 2003, 124, 1166) 및 전해질을 대체 하려는 연구(JACS, 2004, 126, 7164)등 모든 분야에서 탁월한 연구 그룹이다.
브라질의 Paoli 그룹은 2001년 액체전해질을 고분자를 이용하여 고체전해질로 대체한(Adv. Mater. 2001, 13, 826) 독창적인 연구그룹이다.
일본 일본과학기술종합소의 Arakawa 연구팀은 유기고분자를 이용한 홀전도체와 전해질 개발(Adv. Funct. Mater. 2005, 15, 246)에 탁월한 그룹이다.
미국 NREL의 Frank 그룹, 영국 Imperial College의 Durrant 연구팀, 스웨덴 Uppsala 대 Hagefeldt 그룹 등 전 세계적으로 연구(Chem. Rev. 1995, 95, 49)가 활발히 수행되고 있다.
유럽의 EUROCIS 팀과 미국의 NREL 연구팀은 변환효율의 향상하여 xEUROCIS 팀이 1993년에 효율 15%를 달성하였고 이후 NREL은 1994년에 15%를 돌파하고 1999년에는 18.8%를, 그리고 2003년에 19.2%를 거쳐 2008년에 최고 기록인 19.9%를 달성하였다.
CIGS 태양전지 실험실 셀에서 관측된 NREL의 19.9%는 비정질 실리콘, CdTe 등 일부 실용화되어 있는 여타 박막 태양전지에 비해서도 높을 뿐만 아니라 기존의 다결정 실리콘 태양전지의 최고효율 20.3%에 근접하는 것으로, 제조방법에 있어 약간의 차이는 있으나 최고의 효율은 위에서 설명한 금속원소의 동시증발법(co-evaporation)으로 제작된 셀로서 아직까지 모듈 효율이 실험실 제작 태양전지의 효율에 비해 많이 낮아 대규모 상업화까지에는 앞으로도 많은 기술개발이 필요한 실정이다.
CIGS 태양전지는 주로 독일, 일본, 미국 등의 선진 국가의 다수의 업체에서 상용화 중으로 2009년부터 양산화 본격적으로 시작하여 시장이 형성될 것으로 보인다. 태양전지 시장에서 CIGS가 차지하는 비중은 현재 약 5% 이하에 불과하지만 원가 절감의 잠재력이 높아 앞으로 시장 점유율을 비약적으로 높일 가능성이 높다.
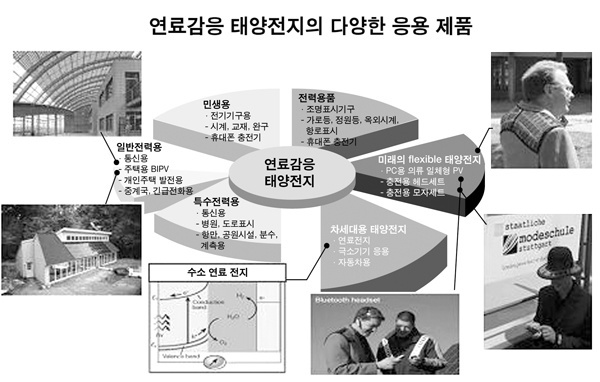
2001년부터 미국의 National Renewable Energy Laboratory를 중심으로 여러 연구기관에서 여러 종류의 탠덤구도에 대해 이론적 및 실험적 연구결과를 제시하고 있다.
Si:H/CIS 구조의 탠덤셀(셀효율 15.6%): PVSC1988, 1384(1998)를 비롯하여 스위스에서는 염료감응/CIGS 구조 탠덤셀(셀효율 15%): Appl. Phys. Lett. 88, 203103(2006)을 제시했고 일본은 25% 효율의 박막태양전지기술을 2020년까지 달성하는 목표를 세운 바 있다(참조: The Japanese PV Roadmap until 2030).
CIGS계 태양전지에서 독성물질인 Cd을 사용하는 CBD 기반의 CdS 버퍼층을 대체하기 위하여 다양한 연구방법이 진행되고 있다. 많은 연구그룹에서 CIS/CIGS 화합물계와 투명전극층으로 사용되는 ZnO 사이에서 격자상수와 에너지 밴드구조의 차이를 줄여주기 위하여 CIGS 흡수층과 연관된 Sulfide/Selenide 계 기반의 버퍼층과 ZnO window 층과 연계된 버퍼층 물질에 대한 연구가 주로 이루어지고 있다. 독일의 HMI(Helmholtz Centre Berlin for Materials and Energy)는 연구중심 기관이지만 법적으로는 GmbH(limited liability company) 정부가 90% 투자를 한 기업형태로 운영된다. 휘어지는 CIGS 태양전지 27cm2 면적에서 15%, 100cm2 면적에서 12.4%의 효율을 보고했다.
미국의 NREL은 2008년 3월에 상용화된 실리콘 기반의 태양전지와 경쟁이 가능한 수준의 박막형 태양전지 제조에 성공했음을 밝힌 바 있다. 3stage 동시진공증발 공정을 활용하여 CIGS 박막 태양전지의 변환효율 19.9%를 달성한 바 있으며 최근 박막 두께를 1.0μm로 낮춘 상태에서도 17.1%의 효율을 달성하였다. CIGS 박막태양전지 기술에 있어서 세계최고효율 기록을 보유하고 있을 뿐만 아니라, 진공증발법, 스퍼터링, 나노분말법, 전착법 등 거의 전 공정에 대한 레퍼런스가 되고 있다.
1980년 III-V 화합물 반도체 태양전지 연구가 시작되어 매년 변환 효율 1% 증가하고 있고 2007년 Spectrolab에서 InGaP/ InGaAs/Ge 태양전지로 40.7%(AM1.5, 240 suns) 효율을 얻었다.
국내 현황
국내 태양전지 분야는 다른 분야 대비 기술수준이 선진국 수준에 가까운 편이나 아직까지 국내에서는 단결정 태양전지의 소량생산만이 가능한 상황이다. 현재 삼성SDI, KPE, 네스코쏠라 등의 회사가 태양전지 생산능력을 확보하고 있으나 생산 규모가 작고 가격경쟁력이 열위에 있어 본격적인 수익을 내지 못하고 있다.
국내 태양광발전 산업의 기술 수준은 폴리실리콘 원료 분야와 박막태양전지, 그리고 제조 장비분야에서 선진국대비 매우 취약한 것으로 평가된다. 선진국 대비 국내 태양전지 산업의 기술 수준은 실리콘 태양전지가 72%, 박막 태양전지 66%, 축전지 77%로 비교적 타 태양광 산업 대비 양호한 수준을 나타내고 있음. 그러나 축전지를 제외한 나머지 전지의 국산화율은 국내 전체 태양광 산업 평균 이하를 나타낸다.
그동안 벌크형 태양전지로의 투자가 주를 이뤄왔으나, 최근 한국철강 및 LG전자 등의 업체들을 중심으로 박막형 태양전지에 대한 투자가 진행되고 있다. 한편 국내에 산업기반이 이미 형성된 단결정 기판 및 태양전지, 결정계 실리콘 태양전지 모듈 등의 부문에서는 타 부문 대비 기술력이 높은 것으로 평가된다. 상대적으로 기술수준이 높은 기판, 실리콘 태양전지, 모듈 등의 분야의 제작 및 생산에 있어서는 국산화율이 70∼80%로 높게 나타났으나 그 이외에 폴리실리콘 원료 제조 분야 및 박막형/다결정 태양전지, 건물일체형 태양전지(BIPV) 모듈 분야에서의 기술개발은 시급한 상황이다. 국내의 경우 염료감응 태양전지를 아직 상품화 목표로 개발하는 기업은 없으나, 삼성 SDI 및 LG 화학 등의 대기업에서 연구개발에 높은 관심을 보이고 있으며 일부 기업에서는 산업화를 모색하고 있다.
국내에서는 국가출연연구소인 KIST(한국과학기술원), ETRI(한국전자통신연구원) 및 KRICT(한국화학연구원)에서 주도적으로 연구를 수행하고 있다. ETRI연구팀은 다공성 나노 TiO2 반도체 전도성 산화막의 개질 개발에 중점을 두고(Langumir 2004, 20, 4246) 연구를 수행하고 있으며 2000년에는 고효율 염료감응 태양전지를 개발하는데 성공했으며. 최근에는 Flexible 염료감응 태양전지를 구현하는 데 성공했다.
ETRI는 2004년에 투명 염료감응 태양전지 개발에 성공하였고 2005년에는 한국전자통신연구원(ETRI)에서 한쪽 면에는 스테인리스 스틸 소재를, 다른 면에는 플라스틱 소재를 사용해 일반적으로 유리 소재를 사용하는 염료감응형 전지에 비해 구부러지는 특성을 갖는 염료감응형 태양전지를 개발하였다.
KIST연구팀은 세계최고효율(4.5% at 100MW/cm2)의 고분자전해질 염료감응 태양전지(Adv. Mater. 2004, 16, 1753; Chem. Commun. 2004, 1662)을 개발하는데 성공했다.
KRICT연구팀은 고효율 dot cell을 개발했다. 또한 기업체와 고려대, 카톨릭대, 한양대, 및 인하대 등 몇몇 대학에서 기초 연구를 수행하고 있다. 2004년에 한국전기연구원은 탄소나노튜브를 이용하여 염료감응 태양전지의 광발전 효율을 9.6%까지 향상시키는데 성공하였다.
고대(세종) 연구진은 염료감응형 태양전지의 세계 최고의 광발전 효율을 발현하는 유기염료를 개발하여 화학분야에서의 최고 권위지에 보고하였으며 이 염료의 장점은 광발전 고효율뿐만 아니라 광안정성 및 열안정성이 뛰어나기 때문에 실용화에 근접한 염료로 세계적으로 인정되고 있다(J. Am. Chem. Soc. 2006, 128, 16701 & Angew. Chem. Int. Ed. 2008, 47, 327).
한국에너지기술연구원이 KAIST 연구팀과 공동으로 모든 단위 박막을 형성할 수 있는 장치를 구축하여 3단계 동시증발법 공정으로 실험실에서 소면적 CIGS 태양전지에서 효율 18.3%를 달성했다. 이 기술은 2007년부터 LG마이크론으로 기술이전이 진행 중이다. 이원화합물의 동시증발에서는 효율 13.4%, 동시스퍼터링에 의한 Cu-In-Ga 합금 제조 및 셀렌화에 의한 CIGS 광흡수층 제조에 대한 공정 연구도 일부 추진되어 9.7%의 효율을 얻고 있다. 나노분말을 이용한 CIS 태양전지 연구 및 탠덤구조에 대한 기초 연구와 고가의 In, Ga을 대체하기 위하여 저가의 Zn, Sn, S를 사용하는 CZTS 박막태양전지기술도 개발을 진행 중이다. 확보된 셀 기술을 바탕으로 모듈 제조를 위한 레이져 스크라이빙 기술 개발을 진행중이며 현재까지 확보된 기술은 아래와 같다.
- 반사방지막 적용한 경우 : 효율 18.3%(0.5cm2)
- 스퍼터링 + 셀렌화 공정 : 효율 9.7%(0.5cm2)
- 그리드 타입 : 효율 10.3%(16cm2)
- 배선 모듈 : 효율 4.7%(16cm2)
ETRI는 2008년부터 내부과제로 동시 진공증발 공정을 활용하여 CIGS 박막태양전지 제조기술을 개발하고 있으며 현재 18%(자체 분석) 정도의 효율을 기록하고 있다. 또한 CuGa, In 타겟을 이용한 스퍼터링 공정을 병행하여 개발 중이며 2009년 4월부터 얇은 박막층을 가지는 CIGS 박막태양전지가 국책과제로 진행 중이다.
영남대학교는 2007년부터 대구테크노파크 나노부품실용화센터와 공동으로 동시증발법을 이용한 CIGS 박막태양전지(100x100mm2) 제조기술을 개발하고 있으며 현재, 10%(자체 분석) 정도의 효율을 기록하고 있다. 또한 CuGa, In 타겟을 이용한 스퍼터링공정을 병행하여 개발 중이며 3차원 투명전극 어레이를 이용하여 pn 접합면적을 극대화하기 위한 소자기술 개발을 진행 중이다.
1997년~1999년까지 산자부 재원으로 에너지 연구원과 KIST에서 소규모로 III-V 화합물 태양전지 연구 후 중단됐다.
KIST에서 기초 연구를 위한 AlGaAs/GaAs 이종계면 태양전지 기술(효율 13.7%) 및 InGaAs/GaAs 양자우물 태양전지(효율 15.2%) 개발(1997년~1999년)했으며 2002년에는 MBE를 이용한 InGaAsN 박막 제조 기술 개발 연구 수행했다. 2003년 한국전자통신연구원에서 양자점을 이용한 광소자 개발 연구: 1.3㎛, 1.5㎛ 양자점 레이저 개발했으며 2005년에는 한국전자통신연구원에서 광통신 소자를 위한 III-V 화합물 반도체 인프라를 이용하여 III-V족 화합물 반도체 태양전지 연구개발 시작했다. 2006년 한국전자통신연구원 독자 기술로 변환효율 21%(AM1.5, 1sun)의 GaAs 단일 접합 태양전지 개발했으며 2007년에는 국내 최초로 한국전자통신연구원에서 변환 효율 23.7%(AM1.5, 1sun)의 InGaP/ GaAs 2중 접합 태양전지를 개발했다. 2008년 KANC에서 24% InGaP/GaAs 2중 접합 태양전지 개발한 바 있다.
국내에는 III-V 화합물 반도체를 이용한 LED, LD, PD와 같은 광소자 기술이 발달 되었으므로 이 기술을 태양전지에 접목함으로서 선진국의 기술 수준에 빠르게 도달 할 수 있는 잠재적인 능력을 보유하고 있다.
CIGS 태양전지의 최근 동향 및 전망
CIGS 박막태양전지 분야는 우리에게 특히 연구 개발의 성공기회를 제공하고 있다. 이 기술은 세계적으로 산업화 초기 단계로서 2세대 박막소재 중 가능 유망한 것으로 인정되고 있다. 그러나 아직 여러 기술들이 동시에 개발되면서 뚜렷한 승자가 없는 상황인데 이는 그 성숙도가 상용활용에는 아직 미흡하기 때문이다. CIGS 박막태양전지 기술의 성공은 소재 및 박막 대면적화 기술개발을 통한 저가격화가 핵심이다. 그런데 우리나라는 세계 최고 반도체/디스플레이 기술 보유국으로서 여러 소재, 박막기술, 대면적화, 고효율화 및 신뢰성의 확보에 대한 경험이 풍부하며 이 요소가 우리에게 CIGS박막태양전지 연구 개발의 성공기회를 제공하고 있다.
글: 김제하 / 한국전자통신연구원 박막태양광기술연구팀
www.etri.re.kr
CIGS 태양전지 개발의 필요성
일반적으로 반도체 소재 기반의 태양전지는 p-n 접합을 이루는 반도체 다이오드에 빛을 쪼이면 전자가 생성 되는 광기전효과(photovoltaic effect)를 이용하여 태양광을 직접 전기로 변환하는 소자로 정의할 수 있다. 가장 기본적인 구성 요소로는 전면전극, 후면적극 및 이들 사이에 위치하는 광흡수체 등 3부분으로 구별된다. 이 중 가장 중요한 소재는 광 전환효율의 대부분을 결정하는 광흡수체이며 이 소재에 따라 다양한 종류의 태양전지 기술이 분류된다. 산업적으로는 태양전지의 에너지 전환 효율과 더불어 제조비용에 의하여 3단계로 구별하고 있다.
즉 1세대는 결정형(다결정 및 단결정) Si 태양전지로서 현재 가장 성숙된 기술 분야이고 2세대는 박막형 반도체(a-Si, CdTe, CIGS) 태양전지로서 에너지 전환효율은 다소 떨어지지만 제조 비용이 훨씬 저렴할 것으로 예상되고 있는 차세대 기술이며 3세대는 식물의 광합성과 같은 기존의 반도체와는 메커니즘을 이용하여 광.전 변환을 만들어 내는 유기물 등 신재료 및 신개념 태양전지 기술이다. 이 신개념 소자는 30% 이상의 월등히 높은 에너지 전환효율과 가장 저렴한 생산비용을 예상하는 미래의 기술로서 아직 실험실 수준에 머물러 있다. 일반적으로 1세대 결정형 Si 태양전지 모듈은 약 15~18%의 모듈 효율을 내고 있는 반면, 2세대 박막형 화합물 반도체 7~12% 및 3세대 태양전지는 5% 에너지 전환효율 대를 기록하고 있다.
구리(Cu)-인듐(In)-갈륨(Ga)-셀레늄(Se)의 4원소 화합물 반도체인 CIGS(CuInGaSe2) 태양전지 셀 효율은 2009년 3월 현재 19.9% 로서 박막형 태양전지 중 가장 높은 효율을 보이고 있다[1]. 이는 2원소 화합물 반도체인 CdTe 박막 태양전지의 16% 셀 효율을 보다 월등히 높은 결과이다.
한편, 결정질 실리콘 소재는 단결정과 다결정 셀에서 각각 25% 및 20.3%의 화합물 반도체에 비하여 상대적으로 높은 셀 전환효율을 보이고 있다. 그러나 CIGS가 다결정(폴리) 실리콘 태양전지의 20.3% 와 대등한 수준을 보이는 것은 주목할 만 하다. 또한 박막형 가운데 비정질(amorphous) 실리콘 태양전지의 상용 모듈 효율은 7% 대 수준이다. 최근 비정질 실리콘(a-Si)과 마이크로 결정형 실리콘(μc-Si)을 접합함으로서 10% 대의 전지 모듈 효율향상도 보고된 바 있다.
그러나 태양전지 상용 모듈의 경우 전환효율은 더 큰 차이점을 보이고 있다. (표 1)은 여러 태양전지의 최고 실험실 셀 효율과 최고의 양산효율에 대한 비교를 보여 준다. 결정질 실리콘 태양전지 모듈이 이미 셀 전환효율의 80% 이상의 높은 전환효율을 보이고 있는 반면 화합물 반도체 기반의 박막태양전지는 상용 모듈의 전환효율이 아직도 50% 수준에 머물고 있어서 실리콘처럼 상용화 수준의 효율에 근접(80%)하기 위해서는 많은 추가적인 기술 개발이 필요한 실정이다.
제조 과정에서도 1세대 실리콘 태양전지 모듈을 만들기 위해서는 소재-> 잉곳-> 웨이퍼-> 셀-> 모듈 단계로 제작되는 과정이 필수적으로 필요하다. 반면에 박막형 태양전지 모듈은 보통 유리기판이나 금속 포일(foil) 위에 반도체를 박막 증착함으로써 셀 및 모듈까지 단일 장소에서 일괄 공정으로 마칠 수 있다. 이 점이 두 기술과 가장 큰 공정상의 차이점이다. 이와 같이 단일 집적화 공정을 이용하기 때문에 박막형 태양전지 모듈 제작은 결정형 실리콘 태양전지에 비하여 공정 단계가 약 반수 정도로 짧고 단순하다는 점이 특징이다.
그리고 웨이퍼에 기반한 결정형 실리콘 태양전지에 비하여 화합물 반도체 소재는 기판소재 위에 박막의 형태로 제조가 된다는 점이 다르며 또한 그 제조 비용도 약 50% 정도로 값싸게 만들 수 있다는 점이 부각되고 있다. 이 장점 때문에 박막 CdTe 태양전지를 생산하는 First Solar(미국)가 504MW를 생산함으로써 2008년에 글로벌 생산 2위에 부상하도록 한 원동력이 되었다. 이는 570MW를 생산한Q-cell(독일)을 제외한 많은 결정형 실리콘 태양전지 생산업체를 뒤로한 결과이다. 그러나 생산의 단순성이라는 기존 장점을 바탕으로 상용화가 되고 있지만 박막 태양전지는 결정형 대비 상대적으로 낮은 효율, 화합물 반도체 소재의 Cd 독극성 재료사용과 에너지 전환 효율향상의 어려움 등이 예상되면서 미래의 유망 산업기술로서만 인정을 받고 있는 실정이다.
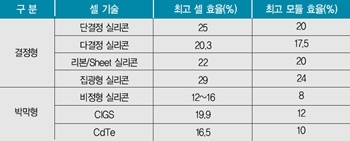
표 1. 여러 태양전지 기술의 최고 셀 및 양산모듈 효율 비교
한편, 화합물 반도체 박막 태양전지 소재인 CIGS는 직접천이 반도체 화합물이기 때문에 태양광 에너지 전환 효율이 좋다. 네 가지 원소 화합물에 Ga, Al, S 등의 원소를 도핑 함으로써 인위적인 밴드갭 조작이 가능하며 그 에너지 갭을 1.0~2.7eV까지 광대역으로 변환할 수도 있어서 광변환효율을 향상시킬 수가 있다. 또한 이 소재의 기반인 CIS(CuInSe2)는 광흡수계수가 105cm-1 로서 광흡수소재 중 가장 높은 특징이 있어서 얇은 광흡수체 박막을 이용해도 동일한 효율을 낼 수 있는 장점이 있다. 또한 환경 안정성과 방사선에 대한 소재의 저항력도 매우 강하다.
그렇지만 핵심 원소인 인듐의 가격이 너무 높아 대량 생산에 불리하고 2원소 박막 태양전지(CdTe)에 비하여 제조공정이 복잡하다는 단점이 있다. 따라서 핵심 소재로 남아있기 위해서는 인듐 및 카드뮴 사용을 하지 않는 소재 발굴과 제조 비용절감을 위한 공정 최적화가 반드시 필요하다. 특히, 4가지 원소를 동시에 사용하기 때문에 조성제어가 까다롭다. 현재 CIGS 박막을 얼마나 효율적으로 제조할 수 있는가 하는 것은 연구개발의 가장 핵심이 되고 있으며 CIGS 회사들은 각자의 CIGS 고유 증착기술로 산업화에 나서고 있는 중이다.
본 기술에서는 가장 고효율을 보이고 동작환경에서 안정적인 화합물 반도체 CIGS 박막 태양전지의 기술과 산업의 동향과 전망을 살펴보기로 한다.
CIGS 태양전지의 구성 및 특성
그림 1은 CIGS 태양전지의 구조도이며 각 층의 명칭과 대표적인 제조 방법을 요약한 것이다. 가장 일반적인 구성으로 소다라임 유리기판 위에 Mo 후면전극, p-형 반도체 광흡수층(CIGS), n-형 반도체 CdS 버퍼층, intrinsic-ZnO/Al 도핑된 ZnO 투명창층, MgF2 무반사층과 그리드 전극(Al/Ni)을 형성하여 제작한다.
이 중 가장 중요한 요소는 빛을 흡수하는 CIGS 혹은 CI(G)S 광흡수층 소재이다. 이 CuIn(Ga)Se2(CIGS)는 CuInSe2(CIS)의 3원소(ternary) 반도체에 갈륨(Ga) 원소를 In치환으로 도핑하여 효율을 증가시킨 것이다.
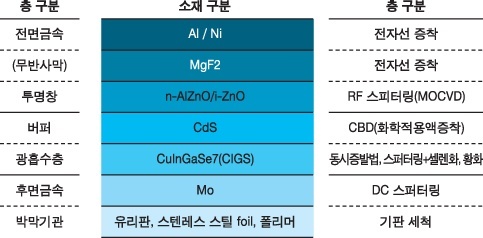
그림 1. CIGS 태양전지의 구조도
네 가지 원소를 사용하고 있기 때문에 조성비의 정확성이 태양전지 효율에 직접적인 영향을 준다. 가장 바람직한 CIGS 비율은 Ga/(In+Ga) = 0.3, Cu/(In+Ga) = 0.8~1.0로 알려져 있다. 특히, Ga이 In의 위치를 치환하여 첨가되면 CIGS의 밴드갭이 향상 되어 소자의 에너지 변환효율도 같이 상승하는 모습을 보이게 된다. 그러나 그 비율이 Ga/(In+Ga) > 0.30 으로 도핑이 증가 되면 밴드갭은 향상될 지라도 효율이 오히려 감소하게 된다. 셀레늄 대신 황(Sulfur)으로 대체 하거나(CuInS2) 혹은 황을 같이 사용하는(CuInSeS) 광흡수체도 널리 사용하고 있다.
CIGS의 박막두께는 통상 약 2.0m이다. CIS는 광흡수계수가 105cm-1로서 광흡수소재 중 가장 높은 특성은 얇은 광흡수체 박막을 이용해도 동일한 효율을 낼 수 있도록 한다. 계산에 의하면 0.5m CIGS 층은 입사하는 모든 빛을 흡수할 수 있다. 실제로 AIST에서는 3-단계 동시증발법 CIGS제조 공정으로 0.75m의 두께에서 15.0%의 효율을 얻었으며[2], ETRI에서는 반응성 스퍼터링 방법에 의한 초박막(sub-micron) CIGS 태양전지 셀 연구가 진행되고 있다. In 및 Ga의 희귀성은 장래 산업화의 문제점으로 지적되고 있어서 이 원소를 포함하지 않는 흡수체 연구도 활발하다.
CIGS 다음으로 중요한 역할을 하는 소재는 50nm 두께의 CdS 버퍼층이다. CIGS 박막은 다결정 성장 특성을 보이고 있다. 즉, 표면이 고르지 못하기 때문에 소자를 안정적으로 하기 위해서는 표면을 모두 덮을 수 있어서(conformal coverage) 소자상 결함을 노출시키지 않는 소재 및 박막 증착기술 이 필요하다. 이 해결방안으로 CdS 소재를 화학용액증착(chemical bath deposition; CBD)으로 성막하는 것이 황금율로 알려져 있다. CdS는 CIGS와 투명창층인 ZnO의 큰 밴드갭 차이를 완충(buffer)하는 역할도 한다.
비록 50nm의 CdS를 사용하고 있지만 카드뮴의 독성 때문에 Zn(O, OH)S, In2S3 등 대체 소재 연구가 진행되고 있다. 특히, ZnS를 사용할 경우 UV 영역의 양자효율이 CdS보다 높아 약 8%의 전환효율 추가 향상이 기대되는 것으로 알려지고 있다[3]. 또한 습식 CBD 제조 방법은 진공방식의 인라인 일괄공정에 장애가 되고 있다. 이를 극복하기 위하여 버퍼 소재를 진공 공정 혹은 진공 공정과 함께 사용할 수 있는 박막 성장법의 개발연구가 활발하다.
기판으로는 유리, 스텐레스 스틸 포일, 타이타늄 포일, 폴리머(polyimide; PI) 등 다양한 소재가 사용된다. 가장 일반적으로 소다라임 유리기판이 사용되고 있는데 그 이유는 유리에 함유되어 있는 나트륨(Na)이 CIGS의 다결정 결정립을 크게 하고 이 때문에 전환효율이 향상하기 때문이다.
반면에 유연기판 소재의 경우 일부러 Na 층을 추가하여 CIGS 결정성 향상을 하고자 하는 연구가 진행되고 있다. 지금 상용화 되고 있는 대표적인 유연기판 소재는 스텐레스 스틸 포일과 폴리이미드(PI) 폴리머 소재이다.
후면전극으로 몰리브데늄(Mo) 전극은 CIGS 태양전지의 황금율 중의 하나이다. Mo는 다른 어떤 소재보다 유리기판과의 열팽창계수가 비슷하며, 부착성과 전기 전도도를 동시에 만족 시켜주는 소재로 알려져 있다. 박막 성장을 위해서는 진공증착 DC 스퍼터링을 가장 많이 사용하고 있다.
한편 전면전극으로 I-ZnO/Al:ZnO가 투명창(TCO; transparent conducting oxide)에 사용된다. 박막태양전지의 경우 모노리식 집적화를 하게 되는 데 있어서 투명창은 1m 이상으로 두껍게 성장하기 때문에 전기 전도도와 빛의 투과도를 동시에 최적화 하는 것이 매우 중요하다. 그리고 ZnO의 고유물성인 친수성은 CIGS 태양전지 모듈의 수명에도 직접적인 영향을 준다. 한편 우주공간용 태양전지 모듈에는 TCO 소재로 ITO를 사용하기도 한다.
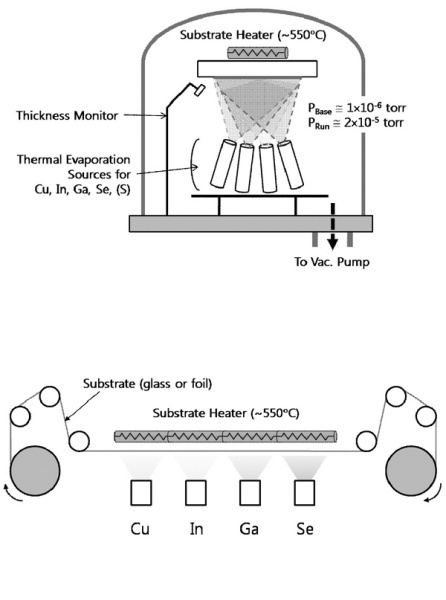
그림 2. CIGS 박막형성기술 (가)동시증발법, (나)인라인증발법
CIGS 박막 성장 및 공정기술
CIGS 태양전지가 고효율 및 대면적 가능성의 장점에도 불구하고 산업화가 부진한 이유는 산업적으로 믿을만한 CIGS 제조공정이 확립되지 못하였기 때문이다. 4원소 화합물인 CIGS는 다양한 제조 방법이 활용되고 있다. 그 종류로는 진공증착, 나노프린팅, 전기증착, CBD 등이 있다. 이 중 가장 많이 활용되고 있는 진공증착 방법으로는 증발법(evaporation)과 2단계공정(two-step process)법 두 가지가 대표적인 공정으로 알려져 있다.
가장 기본적인 증발법은 단위 원소인 구리(Cu), 인듐(In), 갈륨(Ga) 및 셀레늄(Se)을 열 증발원(thermal evaporator혹은 Knudsen cell)을 이용하여 동시에 증발시켜(co-evaporation) 고온 기판에 박막을 형성하는 방법이다. 이는 1982년 Boeing(미국)에서 개발된 방법으로, 각각의 증발원을 독립적으로 설치하여 사용하기 때문에 원소의 조성 제어가 용이하고 특히 도핑 소재인 Ga의 최적 조성비율 Ga/(In+Ga)=0.3을 제어하는데 편리하다.
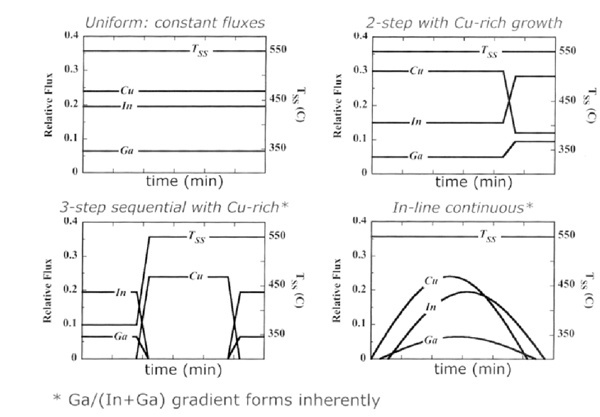
그림 3. 다단계 증발법: (가)single-stage, (나)2-stage, (다)3-stage, (라)in-line
그러나 기본적으로 증발원이 점원(point source)이기 때문에 수천 제곱 센티미터의 대면적 기판에 박막을 형성하기에는 불리한 점이 많다.
따라서 대면적 박막 제작을 위해서는 선형 증발원(line evaporation source)의 개발이 시급한 실정이다. 대면적 박막의 대량 생산을 위해서는 기판이 선형 증발원 위에서 인라인(in-line)으로 수평 이동하면서 박막이 제작되어야 하는데, 이 경우 조성 제어가 정지 상태에서 보다 매우 어려우며, 이는 효율 향상에 가장 큰 장애요인이 되고 있다. 그림 3은 동시 증발법과 인라인법의 비교를 보이고 있다. 산업화에서는 대면적화에 적합한 인라인 증발법이 사용되고 있다. 이제까지 이 방법의 약점으로 많이 지적되었던 것은 점원이기 소재 사용률이 저조하다는 것이었다. 점원의 구조적 특성으로 인하여 상향식으로만 사용될 수 있다는 제약이었다. 그러나 이러한 단점도 선형증발원(최대 1.0m 폭)의 개발로 많이 극복되고 있다.
고효율 태양전지 결정상(-CIGS)을 만드는데 있어서 기판의 온도(보통 550℃)는 매우 중요한 변수이다. 최고 효율의 방법은 박막 증착과 기판의 온도를 3단계로 변화시켜주며 CIGS 결정상(phase)을 최적화하는 3단계 공정법(three-stage process)이다. 이는 1996년 미국 에너지연구소(NREL)에서 개발되었으며 최고 효율인 19.9%를 달성한 방법이다. 그러나 이 방법은 상용화에 적합하지 않기 때문에 기판온도와 증착조건의 단계에 따라 1단계(single stage), 2단계(two-stage) 및 인라인(in-line) 제조가 있다. 그림 4는 4가지 다른 방법을 보이고 있다. 이 중 양산에는 인라인 방법이 양산에 가장 많이 활용되고 있다.
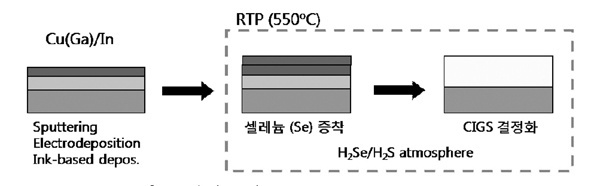
그림 4. 2 단계 공정(two-step process) 구도
2단계 공정(two-step process) 방법은 CIG 혹은 CIGS 전구체(precursor) 제작과 셀렌화(selenization) 혹은 황화(sulfurization)에 의한 제조 공정이다(그림 5). 먼저 전구체 제작에 있어서 스퍼터링에 의한 진공 증착과 전기증착(electro-deposition)에 의한 비 진공법이 있다. 다음으로 전구체의 CIGS 화합물 반도체 조성을 완성하기 위해서 고온 열처리 과정을 거치게 된다. 즉, 증발법이 CIGS증착과 동일한 챔버에서 셀렌화가 이루어지는 것과 달리 2단계 공정(two-step process) 은 독립된 다른 챔버에서 셀렌화가 이루진다는 점이 공정상 차이점이다.
첫 단계에서는 구리(Cu), 인듐(In), 갈륨(Ga) 혹은 셀레늄(Se)이 스퍼터링 증착(혹은 전기도금)에 의하여 순차적으로 기판 위에 전구체 박막으로 형성된다. 다음 단계인 열처리 과정이 이 2단계 공정의 핵심인데 CIGS의 조성을 맞추기 위하여 약 550℃의 고온전기로(furnace)에서 급속 열처리(RTP: rapid thermal process)하게 된다. 이 때 고온 전기로 내부는 하이드라이드 가스(H2Se, H2S) 1atm 분위기에서 400-600℃로 유지되거나 단순히 고온처리 되는 등 공정 노하우는 업체마다 다르다.
사용 소재에 따라 셀렌화(seleniza tion) 혹은 황화(sulfurization)라 불리며 때로는 두 가지가 동시에 사용되기도 한다. 이 방법은 증발법에 비하여 박막의 균일성이 좋고 소재의 활용도도 높일 수 있기 때문에 제작공정의 저가화 가능하다고 알려져 있다. 스퍼터링의 경우 평판형 타겟과 실린더형 타겟은 각각 30% 및 70% 등의 소재 활용율을 보고하고 있다.
반면 전기도금법(ED: electro-deposition)은 90%에 근접한다. 이 방식의 양산화 기술은 1980년대 ARCO Solar(미국)에서 개발되었으며 일본에 기술이 도입되어 Showa Shell에서 대면적 CIGS 모듈 효율 13.4%를 얻은바 있다.
다른 방법으로 CIGS 나노입자를 이용한 잉크프린팅(ink-printing)법(nanosolar)과, 전기화학 증착법(electro-chemical deposition)(IBM) 등이 새로이 연구되고 있지만 이 방법으론 제작된 CIGS셀에서 아직 믿을 만한 전환효율이 보고되고 있지는 못하다. 그러나 이 기술의 가장 큰 장점인 90% 이상의 소재 활용률과 제조 공정의 단순성 때문에 미래 기술로 끊임 없는 관심을 이끌고 있다.
고효율 및 대면적 CIGS 태양전지 모듈을 만드는데 있어서 CIGS 제조공정을 제외한 기타 박막 층은 이미 상용화가 되어 있으며 공정조건도 대부분 확립되어 있다. 아래 표는 CIGS를 제외한 공정이 동일하다고 가정 하였을 때, 여러 가지 CIGS 박막공정의 제조 비용을 비교한 표이다. 표에서 알 수 있듯이 스퍼터링과 전기도금(ED)가 비교적 산업화에 적합한 것으로 나타났다. 그러나 최근 개발된 선형 증발원(폭 1.0m)과 높은 소재 활용율(약 50%)은 증발법이 CIGS모듈 생산의 저가화에 새롭게 경쟁기술로 떠오르고 있음을 예고하고 있다.
CIGS 태양전지 기술과 산업화의 동향 및 전망
위 단락에서 기술하였듯이 CIGS는 가장 효율이 높은 화합물 반도체 태양전시 소재이다. 잠재 모듈 효율은 셀효율(19.9%)의 80% 수준인 16%까지 기술개발이 될 것으로 예상되며 그렇게 되면 셀 최고효율이 16%인 CdTe 박막태양전지와 20.3%인 다결정 실리콘 태양전지 시장을 압도할 것으로 전망한다. 이러한 기대감 때문에 CIGS에 대한 산업화가 많은 관심을 보이고 있는 것이다. 2009년 현재 수준으로 CIGS태양전지의 구조 및 제조 방법 등이 이미 성숙 안정화 돼 가고 있기 때문에 전 세계적으로 CIGS 기업이 속출하고 있다. 이런 상용화의 핵심은 CIGS 박막의 제조방법에 의하여 구분되고 있다. 아래(표 2)는 각 CIGS 기업의 양산수준과 고유 기술을 보인다.
Showa Shell(일본)은 3,459cm2의 대면적CIGS 모듈에서 13.4%(스퍼터링 및 셀렌화)를 기록하고 있으며, 한편 ZnS/CIGS에서 15.7%(셀면적 30x30cm2)를 최근 보고하였다. 이 셀에서 MOCVD에 의한 ZnO:B투명창층이 이용되었다[4]. Wurth(독일)은 7,230cm2 크기의 대면적 모듈에서 12%(인라인 증발법)의 모듈 효율을 보고하였다. 대표적인 CIGS 기업의 현황은 다음과 같다. Centrotherm(독일)은 2007년 이후 CIGS 장비의 턴키솔루션(turn-key solution)을 제공하고 있다. 2007년 9월에 Taiwan에서 처음 Turn-key 장비를 제공하였다(SUNSHINE PV). 핵심기술은 CIGS박막 성장으로 스퍼터링을 이용하고 있으며 RTP(rapid thermal process)를 이용하여 샐렌화를 한다. 인라인 공정에서 열처리에 걸리는 시간은 60초라고 한다. 이 회사의 CIGS 기술은 30x30cm2 유리기판에서 2009년 09월 현재 10.3%의 모듈을 제작하고 있다. Heliovolt(미국)은 서로 다른 두개의 전구체를 접합하여 고속 셀렌화를 수행하는 ′FASST(Field Assisted Simultaneous Synthesis and Transfer)′ 공정을 특허기술로 차별화 하고 있다. 이와 같이 전구체+셀렌화 공정을 기반으로 하는 기술의 핵심은 ′신속한 셀렌화′ 이다.
유연기판을 이용한 CIGS 모듈 생산도 약진을 하고 있다. 특히, 건물일체형(BIPV; building integrated photovoltaics)에 적합한 미래기술로서 유연기판 태양전지의 활용도는 막대할 것으로 예상된다. 이 분야의 선도 기업은(표 2)에 나타났듯이 Global Solar Energy(GSE; 미국)이다. GSE는 스텐레스 스틸 포일 기판 위에 인라인 증발법과 롤투롤 공정을 이용하여 CIGS 셀 및 모듈 생산하고 있다. 현재까지 유일한 CIGS 모듈 양산업체이다. Solarion AG(독일)는 폴리머기판(PI)위에 CIGS셀을 제작한다. 핵심기술은IBAD(ion-beam assisted deposition; patented)을 이용한 Se 증착이며 이 방식의 특징은 이온화된 Se을 이용하여 셀렌화를 수행하기 때문에 400℃저온에서도 고품질의 CIGS 박막을 제조할 수 있다는 것이다.
셀 효율은 14%라고 주장한다. 한편 Ascent Solar(미국)은 PI를 기판을 이용하는 것은 Solarion AG와 동일하지만 유연기판임에도 불구하고 모노리식 집적화를 하는 점이 차별화 되고 있다. 이와는 달리 유연 스텐레스 스틸 포일 기판을 사용하고 있지만 SoloPower(미국)는 CIGS 증착방법으로 비진공 전기도금법을 이용하는 유일한 기업이다. 2008년 약 1.0m2, 9.5%의 효율의 모듈을 제작하여 NREL의 공인을 받은 바 있다.
Solyndra(미국)는 유리기판과 증발법을 이용하지만 모듈의 형상이 원통형을 이용하는 것이 차별화 되어 있다(그림 6). 이 원통형 모듈은 표면으로부터 반사된 빛을 이용하여서도 전력을 만들어 낼 수 있다는 것을 특징으로 하고 있는 특허기술이다.
I(미국) 의 핵심 기술은 ′Ink based CIGS′이다. CIGS 조성을 미리 설정된 분자량 조합으로 전구체(prefix)를 이용하여 물을 이용한 용액잉크를 제조한다.
이 방법에 의하면 잉크의 95%가 평균 결정립의 크기가 100~150nm인 최종 CIGS 가 형성된다고 주장한다. 이 과정에서 포스트 셀렌화(post selenization)는 1기압 H2, H2Se 분위기에서 상압 전기로에서 열처리함으로써 수행한다. CIGS셀은 Mo 포일 기판에 제작하였으며 10cmx10cm, 6~7% 모듈 효율 기술을 보유하고 있다. 향후 모듈 목표 효율은 8~10%이다. 잉크 프린팅 기술을 이용하고 있으나 롤투롤 공정을 하고 있지는 않다.
미국 에너지연구소(NREL)는 3단계 동시증발법에 의한 0.45cm2 CIGS 셀에서 19.9%의 효율을 확보하고 있다. 일본의 AIST는 0.75m CIGS 두께에서 15.0%의 효율을 발표하였다. 이 연구의 CIGS 성장방법은 3-단계 동시증발법을 이용하였다. CIGS의 두께가 2.0m로부터 0.6m까지 줄어듦에 따라 박막의 Ga 조성변화가 달라짐으로써 양자효율(QE; quantum efficiency)이 작아지는 것을 관측하였다[2].
한편 Aoyama Gakguin Univ.에서는 PI 기판을 이용하여CIGS/ZnS(O, OH) 버퍼를 이용한 셀에서 15%의 효율(무반사막 코팅 없이)을 얻었다. 특기할 점은 PI의 동시증발법에서 사용된 기판 온도가 480℃에서 CIGS를 증착하였다[5]. Univ. Stuttgart, ZSW는 CdS/i-ZnO 를 ZnS(O, OH)/ZnMgO 으로 대치하는 새로운 시도를 하였다[3]. CIGS/ZnS/ZnMgO 태양전지는 낮은 파장의 빛을 받아들이는 양자효율이 약 8% 상승하는 효과가 있기 때문에 결과적으로 1~2%의 전환효율 향상을 기대할 수 있다. 이 연구에서 0.5cm2 셀에서 무반사 코팅이 없는 조건으로 18.0%의 효율이 보고되고 있다.
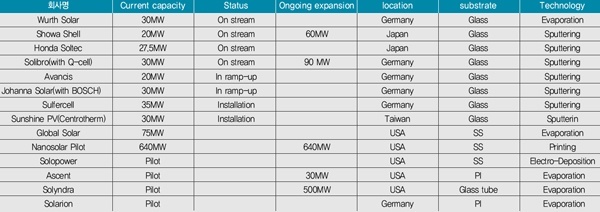
표 2. 2009년도 유럽 및 세계의 CIGS 태양전지 양산 현황
국내 CIGS 박막태양전지 산업은 많은 기업이 사업화를 고려하고 있지만 현재 공식 양산 사업화를 추진하고 있는 곳은 많지 않다. ′LG 이노텍′이 한국에너지기술연구원(KIER)에서 개발된 증발법을 기반으로 유리기판 대면적 CIGS 태양전지 모듈 기술 국책사업을 수행하고 있다. ′텔리오솔라′는 미국의 IEC(Institute of Energy Conversion)연구소와 기술 이전 라이선스 계약을 체결하고 2008년 4월 30일 파일럿 라인을 준공하였으며 파일롯 양산을 추진하고 있다.
한편 스텐레스 스틸 포일을 생산하는 ㈜대양금속이 2009년 4월부터 미국의 Veeco의 증발법 기술을 도입하여 유연금속기판 CIGS 태양전지 양산 설비를 구축 중이다. 이외에 국내 대기업에서 자체적으로 CIGS를 연구 중에 있으며 일부 기업에서는 20cm x 20cm 크기의 유리기판에서 10% 이상의 효율을 이미 달성한 것으로 알려져 있다.
국내 연구소의 CIGS 연구는 한국에너지기술연구원(KIER)에서 18.3%의 동시증발법에 의한 CIGS 셀 기술을 확보하였으며 2008년 4월에 CIGS 태양전지 연구를 시작한 한국전자통신연구원에서도 2009년 5월 동시증발법에 의한 16%의 CIGS 셀 기술확보를 발표하였다[6]. 2009년 국책 CIGS 기술 개발 사업의 확대로 KIST, 표준연구원 등 여러 정부출연연구소에서 CIGS와 관련된 연구가 시작되었다. 대학의 CIGS 연구로서는 KAIST의 안병태 교수팀이 가장 오랫동안 수행하였으며 기술적으로도 앞서 있다. 그 동안 KIER과 함께 동시증발법, 스퍼터링 CIGS 증착 등 다양한 기술 분야에서 많은 업적을 쌓았다. 한편, 성균관대학교 정덕영 교수팀은 나노입자 CIGS 제조 및 전기도금법에 의한 셀 제작 연구를 수행해 오고 있다. 그리고 중앙대학교 최인훈 교수팀은 MOCVD법을 이용한 CIGS 증착 기술을 다년간 연구를 수행해 오고 있다. 한편, 새로 영남대학교와 울산과기대 등 젊은 교수팀들이 의욕적으로 연구를 수행하고 있다. 조만간 우리나라의 CIGS 태양전지 연구에 주목할 만한 성과가 예상된다.
그림 7은 2007년에서 2012년까지 파일롯 양산규모(>25MW)를 갖추게 될 박막태양전지 기업들의 증가추세를 보이고 있다. 비정질 실리콘 태양전지가 두드러지는 것은 a-Si 턴키솔루션이 제공되고 있기 때문으로 보인다.
현재 First Solar가 주요 박막생산기업이기는 하지만 소재, 환경유해성, 기술부족 등의 여러 가지 제약조건에 의하여 그 CdTe 태양전지 생산기업은 눈에 띄는 증가가 없는 것으로 전망되고 있으나 최근 Abound Solar의 등장으로 CdTe 태양전지도 성장할 것으로 예상된다. 이 시장전망에 의하면 박막형 태양전지의 산업화는 CIGS와 비정질 실리콘(a-Si) 태양전지가 두 축으로 성장할 것이 예상되고 있다. 그러나 아직도 CIGS 태양전지가 First Solar처럼 시장에 화려하게 등장하기 위해서는 양산기술 면에서 해결해야 할 기술적인 문제가 많이 남아 있다.
제안하고 싶은 정부 정책 반영 안
CIGS 박막태양전지 분야는 우리에게 특히 연구 개발의 성공기회를 제공하고 있다. 이 기술은 세계적으로 산업화 초기 단계로서 2세대 박막소재 중 가능 유망한 것으로 인정되고 있다. 그러나 아직 여러 기술들이 동시에 개발되면서 뚜렷한 승자가 없는 상황인데 이는 그 성숙도가 상용활용에는 아직 미흡하기 때문이다. CIGS 박막태양전지 기술의 성공은 소재 및 박막 대면적화 기술개발을 통한 저가격화가 핵심이다. 그런데 우리나라는 세계 최고 반도체/디스플레이 기술 보유국으로서 여러 소재, 박막기술, 대면적화, 고효율화 및 신뢰성의 확보에 대한 경험이 풍부하며 이 요소가 우리에게 CIGS 박막태양전지 연구 개발의 성공기회를 제공하고 있다.
CIGS 박막태양전지는 산업화 초기 단계로 인식되고 있지만 기술적으로 극복해야 할 과제가 아직도 많은 추가 집중 연구개발이 절실한 분야이다. 효율측면에서도 실험실(20%) 수준이 상용제품(10%)에 비하여 2배 이상의 엄청난 차이를 보이고 있다. 이 수준은 결정질의 경우 상용제품 수준이 실험실의 85% 이상을 차지하는 것에 대비된다. 추가 기술 개발은 여러 소재, 박막기술, 대면적화, 고효율화 및 신뢰성의 모든 분야에 펼쳐져 있다. 그 중 핵심은 CIGS 소재의 박막성장기술이다. 그 외 위에서 설명한 신소재 및 박막기술의 추가 개발은 기술 경쟁력 확보에 필수적이며 지적재산권 확보에 의한 중요성은 차별화 전략에 아무리 강조해도 지나침이 없다.
독자 원천 기술을 개발하기 위하여 소재, 소자와 관한 원천핵심 기술 확보를 위한 단기 및 중기연구를 전문 연구소에서 수행하고 미래지향적인 기초기술의 장기적이고 지속적 개발과 미래 인력양성을 대학에서 확보하기 위한 집중적인 연구 투자가 필요하다. 또한 국내의 한정된 연구인력 만으로는 글로벌 시대의 급진하는 기술개발을 따라잡을 수가 없다. 따라서 해외 CIGS 태양광연구 그룹과의 연구원의 교환 및 공동워크숍 개최, 매칭 펀드에 의한 실질적 국제공동연구의 확대를 요청한다. 이는 국외의 연구 자원을 활용한 국내 기술의 국제화가 향후 이 산업의 지속적 성공에 필수적인 요소이기 때문이다.
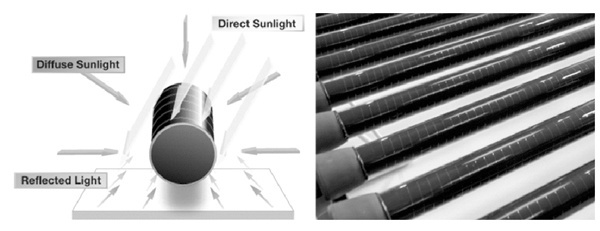
그림 5. 원통형 CIGS 셀 및 모듈(Solyndra)
CIGS 박막태양전지는 산업화 기술이다. 즉, 이 기술을 태양광산업으로 육성하기 위하여 먼저 차세대 주력 에너지 산업기술로 예상되는 박막형태양광 산업육성을 위한 정부 주도의 정책지원이 필요하다. 그 안으로서 국내 태양전지 및 장비 산업체가 필요로 하는 것은 각자 개발된 기술을 검증하고 평가할 수 있는 R&D 파일롯 수준의 공용 팹의 운영을 필요로 하고 있다. 또한, 정부출연 연구소 및 대학과 산업체가 참여하는 공용의 기술교류 협의체 및 공용 시험생산 팹의 운영이 절실하다. 이를 통하여 우리 고유기술을 세계 수준의 박막태양광발전의 신산업으로 육성할 수 있을 것으로 예상한다.
기대효과 및 파급효과
CIGS 박막태양전지는 소재의 우수성으로 지금 박막태양전지의 선두 주자인 CdTe를 제치고 조만간 가장 주요 박막태양전지로 성장할 것을 모두가 예상하는 유망한 분야이다. 이 기술의 개발을 통하여 국가 차세대 박막태양광발전산업의 신성장 동력을 창출을 할 수 있다. 우리나라의 세계일류 반도체/디스플레이 기반 기술을 박막형 태양전지 기술 산업과의 유사성으로 태양광발전 산업 육성에 의한 세계 에너지 시장을 선점과 주도의 가능성을 한층 높이고 있다. 이렇게 함으로써 국가적으로 에너지 안보와 에너지 자주권을 확보할 수 있다. 특히, 최근 국제 아젠다로 부상한 온실가스 감축의 핵심산업이 될 것이다.
두 번째로는 선도적이고 시급한 자체 기술 개발은 해외시장 개척 및 조기 확보할 가능하게 한다. 중동국가들과의 국제협력을 통하여 이 지역시장을 선점할 뿐만 아니라 우리 기술의 대외 경쟁력을 강화할 수 있다. 특히 화석연료(석유) 자원의 고갈에 대응하여 대체 에너지 개발에 열중인 자원 강국 리비아, UAE와 상용화를 통한 공동실험 및 연구 개발을 추진할 수 있다. 중동국가는 양질의 태양에너지 자원 활용의 최적지이며 세계시장을 선점하기 위하여 공동실험을 개발단계부터 전략적으로 추진한다. 이렇게 함으로써 확보된 중동의 태양광시장은 향후 유럽 및 아프리카의 시장 확대진출의 교두보 역할을 할 수 있을 것으로 예상한다.
세 번째로서는 에너지 패키지형 산업창출이다. 미래의 에너지는 유사한 여러 다른 형태의 에너지가 한 네트워크로 결합되는 스마트그리드 기술로 진화할 것이며 이 CIGS 태양전지기술은 그 핵심역할을 수행할 것이다.
또한 상호 보완적 산업의 패키지형 에너지 산업이 가능하다. 즉, 태양광과 수소에너지가 결합한 신시장의 창출이 가능하다. 태양광발전 플랜트와 바닷물의 담수화 및 수소 생산을 연계하는 패키지형 에너지 시장을 진출할 수 있다. 이러한 패키지형 에너지 산업은 이 분야의 미래 기술 개발을 선도하고 블루오션의 신산업 파생 창출이라는 파급효과를 얻을 수 있을 것이다.
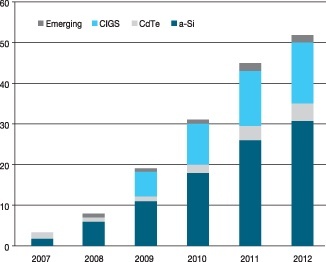
그림 6. 박막 태양전지 양산(>25MW) 업체수의 증가 예측 전
맺는 말
CIGS 태양전지는 가장 효율이 좋은 화합물 반도체로서 향후 박막태양전지 시장의 지배적인 기술이 될 것이다. 그러나 안정적인 고품위 CIGS 대면적 박막 성장은 아직도 기대에 못 미치고 있으며 최고 실험실 셀 효율과 대면적 모듈간의 효율 격차도 50% 수준에 머물러 있는 등 기술의 성숙도가 낮은 편이다.
CIGS 태양전지 R&D는 단위 첨두전력(Wp)당 생산 비용(cost)를 저감하는 것을 가장 중요한 목표로 지향하고 있다. 이 목표를 달성하기 위하여 필요한 것은 전환효율 향상, 태양전지모듈의 저가화, 긴 수명 등이다. 세계적으로 CIGS는 어느 한 순간에도 선도기업이 탄생할 수 있는 여건을 지금 갖추고 있다. 그러나 아직도 CIGS 박막 제조기술을 포함하여 여러 방면에서 50%의 셀-모듈간 격차만큼 많은 R&D 기회를 보이고 있다.
즉, 전환 효율 향상과 더불어 무독성 재료의 사용, 신소재 TCO 발굴, Solyndra와 같은 새로운 모듈 개념 개발 등에 많은 가능성이 열려 있다. 또한 한국으로서는 상대적으로 상용화 발전이 늦은 유연기판 태양전지 기술도 주목해야만 할 것이다. CIGS 태양전지는 차세대 지배적인 박막태양전지 기술이 될 것이 예상되는 만큼 많은 노력을 기울여 연구할 필요가 있다.
참고문헌
- I.Repins, et. al., Prog. Photovolt: Res. Appl. 2008; 16:235-239
- Y. Kamikawa-Shimizu, et. al., EUPVSEC 2009, 3BV.5.92
- D. Hariskos, et. al., EUPVSEC 2009, 3DO.4.5
- H. Sugimoto, et. al., EUPVSEC 2009, 3DO.6.4.
- T. Nakada, et. al., EUPVSEC 2009, 3DO.4.3
- 김제하 외, 한국재료학회 춘계학술대회 및 제 16회 신소재 심포지움, 2009년 5월 21일
- Greentech InDetail Thin-Film PV 2.0 Market Outlook Through 2012(2008)
회원가입 후 이용바랍니다.
개의 댓글
댓글 정렬
BEST댓글
BEST 댓글
답글과 추천수를 합산하여 자동으로 노출됩니다.
댓글삭제
삭제한 댓글은 다시 복구할 수 없습니다.
그래도 삭제하시겠습니까?
그래도 삭제하시겠습니까?
댓글수정
댓글 수정은 작성 후 1분내에만 가능합니다.
내 댓글 모음