[아나로그디바이스=브랜든 허스트(Brandon Hurst) FAE]
▶개요
이 글에서는 트루 와이어리스 스테레오(TWS : True Wireless Stereo) 이어버드 애플리케이션을 위한 전원 아키텍처 에뮬레이팅용 레퍼런스 디자인을 설명한다. 이를 통해 설계 엔지니어가 자신이 개발하는 애플리케이션의 충전 속도를 약 4배 더 빠르게 하면서 솔루션 크기와 시스템 BOM 비용을 낮출 수 있는 방법을 소개한다. 서미스터와 열화상 측정을 이용한 테스트 결과 이 솔루션이 기존 솔루션에 비해 온도가 낮다는 것을 확인할 수 있다. 이 레퍼런스 디자인은 SIMO(Single-Inductor, Multiple Output) 아키텍처에 자율 헤드룸 추적(Autonomous Headroom Tracking) 기능을 적용한 솔루션이 제공하는 다양한 이점을 보여준다.
▶머리말
웨어러블 디바이스가 혁신을 거듭함에 따라 견고한 전원 아키텍처에 대한 요구가 계속해서 높아지고 있다. 지난 십여 년 동안 웨어러블 헬스 모니터링 시장은 빠른 속도로 성장해 왔으며 이들 디바이스의 차세대 제품들은 전과 동일한 초소형 크기에 더 많은 기능들을 포함하게 될 것이다. 오늘날의 웨어러블 디바이스는 통상적으로 와이파이, 블루투스, 생체 징후 모니터링(VSM : Vital Sign Monitoring) 같은 기능들을 포함해야 한다. 여기에 점점 더 많은 기능을 포함하려면 시스템 레벨 및 IC 레벨 설계 엔지니어들은 웨어러블 디바이스 전원과 관련하여 현명한 선택이 필요하다.
▶무선 이어버드용 전원과 관련한 과제들
오늘날 트루 와이어리스 스테레오(TWS) 이어버드 애플리케이션은 크기가 제한된 작은 솔루션에 여러 개의 레귤레이터를 포함해야 하며 궁극적으로 최종 시스템은 주머니 안에 쏙 들어가도록 설계돼야 한다.
<그림 1>은 TWS 이어버드 애플리케이션의 통상적인 전원 시스템을 보여준다. 크레이들과 이어버드 간에는 DC-DC 컨버터가 사용돼 전압을 VSYS에서 5V USB 레벨로 높인다. 이렇게 하면 이어버드의 리니어 차저가 드롭아웃을 하지 않도록 충분한 헤드룸을 제공할 수 있다. 그러나 이 솔루션의 단점은 이어버드 리니어 차저 FET에서의 드롭아웃 전압과 손실 때문에 효율 손실이 크다는 것이다. 이어버드 배터리의 충전이 부족한 상태일 때는 특히 그렇다. 낮은 효율로 충전이 이루어지면 열 발생이 높아지고 이는 시스템 배터리 수명의 단축과 신뢰성 저하로 이어진다.
![그림 1. TWS 이어버드 애플리케이션의 통상적인 전원 아키텍처 다이어그램 [자료=ADI]](https://cdn.epnc.co.kr/news/photo/202402/240489_242665_015.jpg)
경우에 따라서는(그림 2) 시스템 효율을 높이기 위해 전력선 통신(PLC : Powerline Communication)을 추가할 수 있다. 그러면 크레이들 측의 벅-부스트 레귤레이터의 도움을 받아 리니어 차저의 헤드룸을 추적할 수 있다.
하지만 웨어러블 제품은 솔루션 크기가 무엇보다 중요하다. 기존의 이들 크레이들 및 이어버드 솔루션은 모두 웨어러블 디바이스의 주변장치에 전원을 공급하기 위한 벅 출력이 필요로 하는 인덕터와 PLC 칩이 제품의 크기와 비용에 직접적인 영향을 미친다.
![그림 2. PLC를 추가한 TWS 이어버드 애플리케이션의 통상적인 전원 아키텍처 다이어그램 [자료=ADI]](https://cdn.epnc.co.kr/news/photo/202402/240489_242666_039.jpg)
▶최선의 솔루션은 SIMO 아키텍처와 자율 헤드룸 추적
SIMO 전력 관리 IC(PMIC)는 콤팩트한 디자인 요구를 충족하기 위해 요구되는 아키텍처와 효율을 제공한다. 배터리로 구동되는 웨어러블 애플리케이션들 역시 ‘자율 헤드룸 추적’이라 불리는 기술의 이점을 누릴 수 있는데 이 기술은 배터리 충전 회로에 대한 전압 강하를 최소화하면서 충전 전류를 레귤레이트할 수 있는 최적의 헤드룸을 제공한다. 이는 추가적인 부품 사용 없이도 충전 회로에서 전력 손실과 열 발생을 줄이며 그럼으로써 웨어러블 디바이스가 충전하는 동안 온도를 낮게 유지하고 더 빠르게 충전할 수 있게 해준다.
MAX77659는 웨어러블 소비가전 및 의료용 기기에서 효율을 높이고 시스템 보드 공간과 BOM 크기를 줄이기 위해 설계된 SIMO PMIC이다. 이 PMIC는 동일한 인덕터를 사용해서 최대 90%의 효율로 3개의 벅-부스트 출력을 제공한다. 또한 VSM 같이 높은 PSRR(Power Supply Rejection Ratio)을 필요로 하는 민감한 애플리케이션을 위해서 추가적인 LDO 레귤레이터도 포함한다. 게다가 SIMO 아키텍처는 효율면에서 근본적으로 유리하며 최소한의 솔루션 크기로 극히 낮은 대기 전류를 제공할 수 있다.
MAX77659의 자율 헤드룸 추적 기능은 SIMO 출력 중의 하나를 사용해 배터리 충전 트랜지스터에 대한 전압 강하를 최소화함과 동시에 충전 전류를 레귤레이트하기 위한 최적의 헤드룸을 제공한다. 그 결과 이 트랜지스터에서 전력 손실을 줄이고 열 발생을 낮추는데 여기에는 어떠한 추가 부품도 필요치 않다. <그림 3>은 급속 충전 프로세스 전반에서 자율 헤드룸 추적이 어떻게 이루어지는지 보여준다.
![그림 3. 리튬이온 배터리 충전 사이클에서 자율 헤드룸 추적 [자료=ADI]](https://cdn.epnc.co.kr/news/photo/202402/240489_242667_15.jpg)
▶MAX77659 레퍼런스 디자인
<그림 4>의 레퍼런스 디자인은 MAX77659 SIMO PMIC 솔루션과 통상의 리니어 차저 솔루션을 비교해서 보여준다. MAX77659 SIMO PMIC는 자율 헤드룸 추적 기능을 포함함으로써 기존 솔루션(그림 4, 크레이들 B)에 사용되는 벅-부스트 레귤레이터를 제거할 수 있다(그림 4, 크레이들 A). 이는 충전 효율을 높임으로써 전반적인 시스템 배터리 수명을 향상하고 솔루션 크기와 BOM 비용을 줄일 수 있게 한다.
![그림 4.TWS 이어버드용으로 제안된 솔루션과 기존 솔루션을 비교하는 레퍼런스 디자인의 블록 다이어그램 [자료=ADI]](https://cdn.epnc.co.kr/news/photo/202402/240489_242668_136.jpg)
<그림 5>는 MAX77659 레퍼런스 디자인의 전체 PCB 모습을 보여준다. 이 레퍼런스 디자인은 두 쌍의 크레이들/이어버드 솔루션을 포함한다. 하나는 MAX77659 SIMO PMIC를 사용한 것이고(크레이들/이어버드 A) 다른 하나는 통상의 리니어 차저 디자인으로서(크레이들/이어버드 B) MAX77734 리니어 차저를 사용한 것이다. 베이스 보드의 푸시버튼을 사용해서 A 분기와 B 분기 모두의 충전을 토글할 수 있으며 이어버드의 MAX17260 퓨얼 게이지가 측정한 충전 전류와 온도는 OLED 디스플레이를 통해 볼 수 있다. 이 디스플레이는 차저 상태도 표시하는데, 과열 시 차저가 언제 충전 전류를 낮춰야 하는지를 보여준다.
![그림 5. MAXREFDES1323 레퍼런스 디자인 보드 [자료=ADI]](https://cdn.epnc.co.kr/news/photo/202402/240489_242669_25.jpg)
▶배터리 관리 시스템(BMS) 충전 표준
일본 전자정보기술산업협회(JEITA)는 시스템 및 배터리 마모를 줄임으로써 최종 사용자의 시스템 안전과 신뢰성을 높이는 엄격하고도 강력한 기법들을 제공하는 배터리 관리 시스템(BMS)과 관련한 표준들을 제정하고 있다.
최종 애플리케이션은 배터리 충전의 정전류(CC) 및 정전압(CV) 단계에서 충전 전류 및 전압 레벨을 낮추는 통합 JEITA 보호 기능을 활용하는 것이 일반적이다. 만약 시스템이 너무 뜨거워지면 충전 전류와 전압을 낮춰서 회로가 식을 수 있게 하는 것이다. 이처럼 전류를 억제함으로써 최종 사용자를 보호하고 시스템의 신뢰성과 수명을 유지할 수 있다. 하지만 안타깝게도 충전 전류를 낮추는 것은 충전 속도가 느려진다는 것을 의미하기도 한다. 따라서 JEITA 기능을 포함해야 한다는 게 웨어러블 설계에 대한 부담을 가중시키는 일이 될 수 있다. 이러한 설계 부담을 덜 수 있는 방법 중 하나는 장시간 높은 충전 전류에 노출되면서도 우수한 열 성능을 유지하는 솔루션을 사용하는 것이다.
▶성능 비교
기존 솔루션과 제안한 솔루션의 열 성능을 비교하기 위해 270mA CHG_CC(정상적 CC 전류)와 75mA JEITA_CC(JEITA_WARM 온도 임계를 넘는 CC 전류)로 1분간 충전 테스트를 실시했다. 테스트 목적은 이 기간 동안 온도 차이를 알아보고 두 솔루션에 대해 JEITA 보호 기능을 발동하지 않으면서 더 높은 충전 속도를 유지할 수 있는지 알아보는 것이었다. 반복 재현성(repeatability)이 우수하고 온도 상승을 IC만 경험하는 것으로 격리시킬 수 있다는 점에서 배터리 시뮬레이터를 사용했다. 테스트에 사용한 열 한계는 45도였는데 이는 주변 온도보다 21도 상승하는 것을 의미한다. 이 레퍼런스 디자인의 PCB는 0.0014인치, 0.0007인치, 0.0007인치, 0.0007인치, 0.0007인치, 0.0014인치의 구리 두께로 이루어진 6-레이어 보드다. <표 1>은 테스트 조건을 <표 2>는 테스트 결과를 각각 보여준다.
![JEITA 충전 테스트 조건 [자료=ADI]](https://cdn.epnc.co.kr/news/photo/202402/240489_242671_820.png)
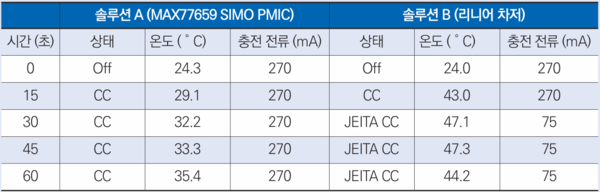
이 테스트 과정에서 MAX77659 SIMO 솔루션은 1분 동안 11.1도 상승했는데 처음 30초가 지나고부터는 온도 상승의 속도가 크게 느려졌다. 제안된 솔루션은 테스트 동안에 어느 시점에도 JEITA 모드가 발동되지 않았다. 기존 리니어 충전 솔루션은 15초 만에 온도가 거의 20도 상승했으며 30초 만에 JEITA 보호가 발동해 충전 전류를 억제했다.
▶열화상 결과
JEITA 보호 기능을 비활성화한 상태에서 열 동작을 알아보기 위해 이번에는 또 다른 테스트로 열화상 카메라를 사용해 SIMO PMIC 솔루션과 리니어 차저 솔루션의 온도를 측정했다. 파라미터들은 첫 번째 테스트와 같았고 JEITA 보호 기능을 비활성화하기만 했다.
![두 차저 솔루션의 열화상 결과 [자료=ADI]](https://cdn.epnc.co.kr/news/photo/202402/240489_242670_316.jpg)
리니어 차저 솔루션은 2분간의 테스트 동안에 온도가 58.1도로 상승한 데 반해 SIMO PMIC의 온도는 단지 37.5도로 상승했다. 이 결과에 따르면 SIMO 솔루션이 리니어 차저 솔루션에 비해 온도 상승을 거의 72% 낮춘다는 것을 알 수 있다.
▶맺음말
이 글에서는 TWS 이어버드 애플리케이션에서 MAX77659 SIMO PMIC와 통상의 리니어 차저 솔루션을 비교하고 스위칭 차저 솔루션으로 자율 헤드룸 추적 기능의 이점을 알아보았다. 테스트 결과를 보면 SIMO PMIC 솔루션이 열을 72%까지 줄임으로써 일반적인 리니어 차저 솔루션에 비해 거의 4배의 충전 전류를 안전하게 유지할 수 있다는 것을 알 수 있다. 이는 시스템이 엄청나게 빠르게 충전을 하면서도 온도를 낮게 유지할 수 있게 함으로써 웨어러블 디바이스의 중요한 과제 하나를 해결한다.
MAX77659 SIMO PMIC는 차세대 웨어러블 디바이스를 위해 안전하고 신뢰할 수 있는 충전 솔루션을 가능하게 함과 동시에 효율을 높이고 필요한 솔루션 크기와 시스템 BOM 수를 줄이도록 한다. 이 외에도 아나로그디바이스는 차세대 웨어러블 디바이스를 위한 동급 최상의 저전력 솔루션으로서 다양한 구성의 SIMO PMIC 및 배터리 모니터링 제품들을 제공한다.
▶저자 소개
브랜든 허스트(Brandon Hurst)는 아나로그디바이스의 필드 애플리케이션 엔지니어(FAE)로서 소프트웨어 및 임베디드 시스템을 맡고 있다. 임베디드 시스템뿐 아니라 배터리 충전 및 퓨얼 게이징과 관련해서 풍부한 경험을 쌓고 있다. 캘리포니아 폴리테크닉 주립대학–샌 루이스 오비스포에서 전기공학 학사학위를 취득하고 2021년 1월에 맥심 인터그레이티드(현재 ADI에 합병)에 입사했다.
그래도 삭제하시겠습니까?